Klinikum Frankfurt Höchst, Germany, found many inefficiencies in its laboratory inventory-management processes – and a way to save time, reduce costs, minimize errors, and streamline regulatory compliance.
Klinikum Frankfurt Höchst cares for 36,000 inpatients and 80,000 outpatients annually. The full-service medical center in the largest municipal hospital network in Germany’s Rhein-Main region constantly improves its processes for providing the highest levels of patient care.Its laboratory provides a diverse array of services: classical clinical chemistry, immunochemistry, infection serology, hematology, hemostasis, blood-bank services, and microbiology testing. It performs 3.6 million tests annually, consuming on average 300,000 tubes and 25,000 cartons of reagents and other testing supplies.
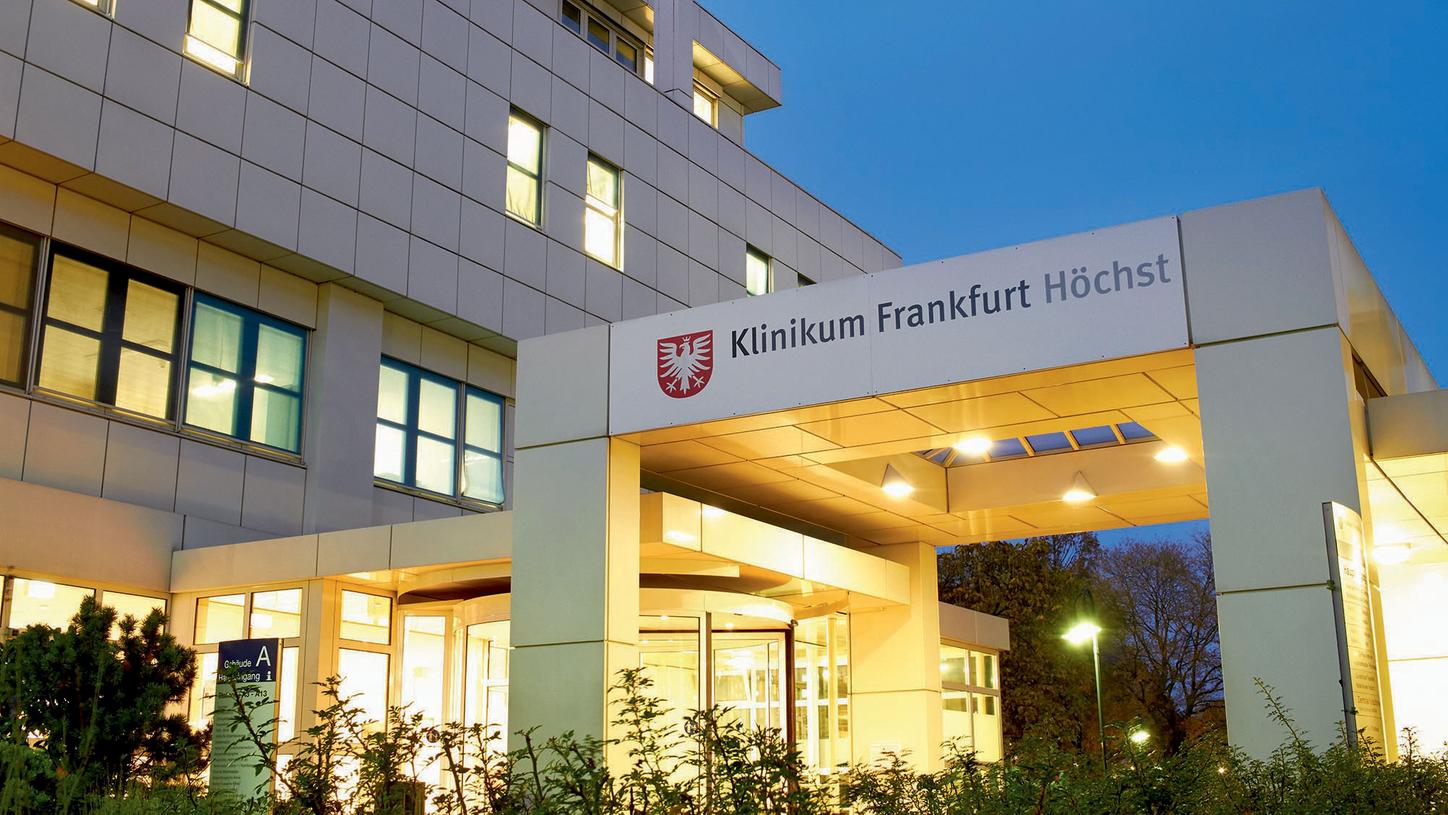
Manual inventory management consumes valuable staff time
When reviewing its laboratory inventory-management processes, it found many inefficiencies. With no centralized order management in place, responsibilities were spread among multiple staff members in the core, serology, and hematology labs. Each highly trained staff member took time away from other professional responsibilities to manually conduct inventory checks and ordering. Among staff members, opinions differed on appropriate minimum stock levels. Coordination and communication regarding inventory were difficult when staff were out on sick leave or time off. In addition, processing the multitude of order documents and tracking product numbers posed a high administrative burden.
In the typical manual inventory model prevalent in most laboratories today, the biggest consumer of time is the counting of boxes – repeatedly – in the refrigerator and on shelves. Then, when an order is required, it is manually composed and submitted. Comprehensive documentation and tracking of inventory is another time-consuming task. This is becoming more important as many regulators are seeking detailed inventory-management documentation.
Klinikum Frankfurt Höchst aimed to free up its lab staff from these tasks and enable them to focus on the high-skill jobs they had been hired to perform. The laboratory wanted to ensure total control over inventory by stocking the right products in the right quantities on its shelves—with all the documentation needed to simplify, and adhere to, regulatory compliance. “Our lab is the central lab for the entire 1000-bed hospital, and we also serve external hospitals and physician offices,” says Dr. Oliver Colhoun, laboratory director at Klinikum Frankfurt Höchst. “We need to deliver fast, high-quality results 24 hours a day, with as little cost and personnel deployment as possible. After achieving good results automating our analytic processes with Siemens Healthineers solutions—including pre- and post-analytics—we realized that the management of consumables still represented a large amount of invested labor. That became the next area we targeted for increased efficiency.”
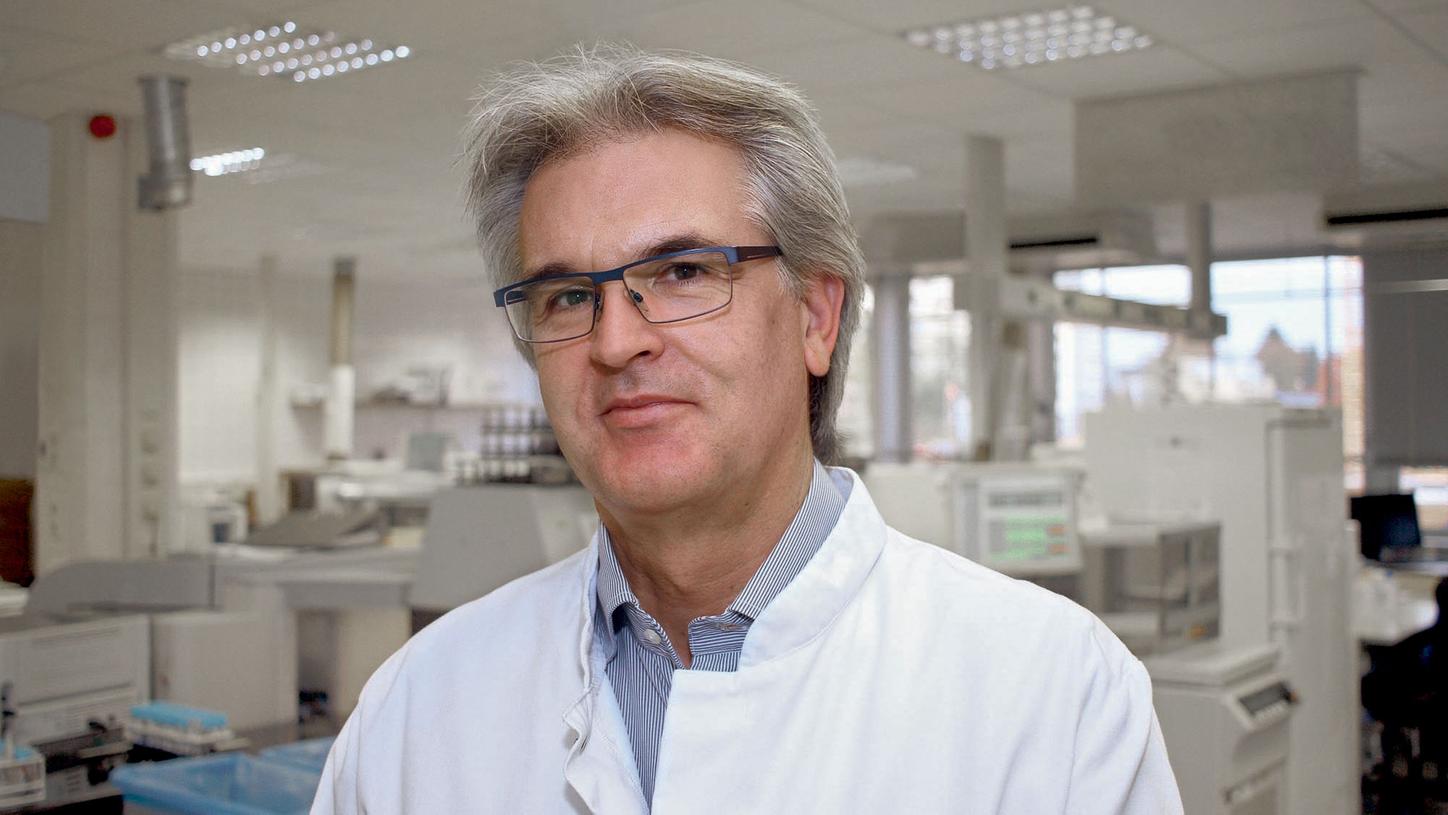
Automating for operational efficiency
At first, the medical center considered a bar-code label system for tracking inventory. Then it learned about a newer, more powerful technology: Atellica Inventory Manager (Atellica IN). Atellica IN is a cloud-based inventory-management system that improves control over all stages of the inventory-management process with an easy-to-navigate dashboard accessible with role-based security from any Internet-connected computer, tablet, or smartphone with a web browser.
Atellica IN uses wireless radio frequency identification (RFID) to automatically track inventory consumption across multiple laboratories in real time. Supported consumables include reagents, calibrators, controls, and ancillary products from Siemens Healthineers or third parties. When items reach critical levels as defined by customized reordering rules, Atellica IN sends email alerts and proposes orders through a cloud-based service. No manual intervention is needed to construct an order. When new products arrive – often within 24 hours – staff members check them in, label them with the received date, expiration date, and lot numbers, and place them into storage locations such as freezers or refrigerators.
“With Atellica Inventory Manager, we work within a structured order process that enables massive time savings for professionals,” Dr. Colhoun says. “We get a total, real-time overview of all items in stock without counting boxes. Atellica IN knows what needs to be ordered, and staff can complete purchase orders at the push of a button.”
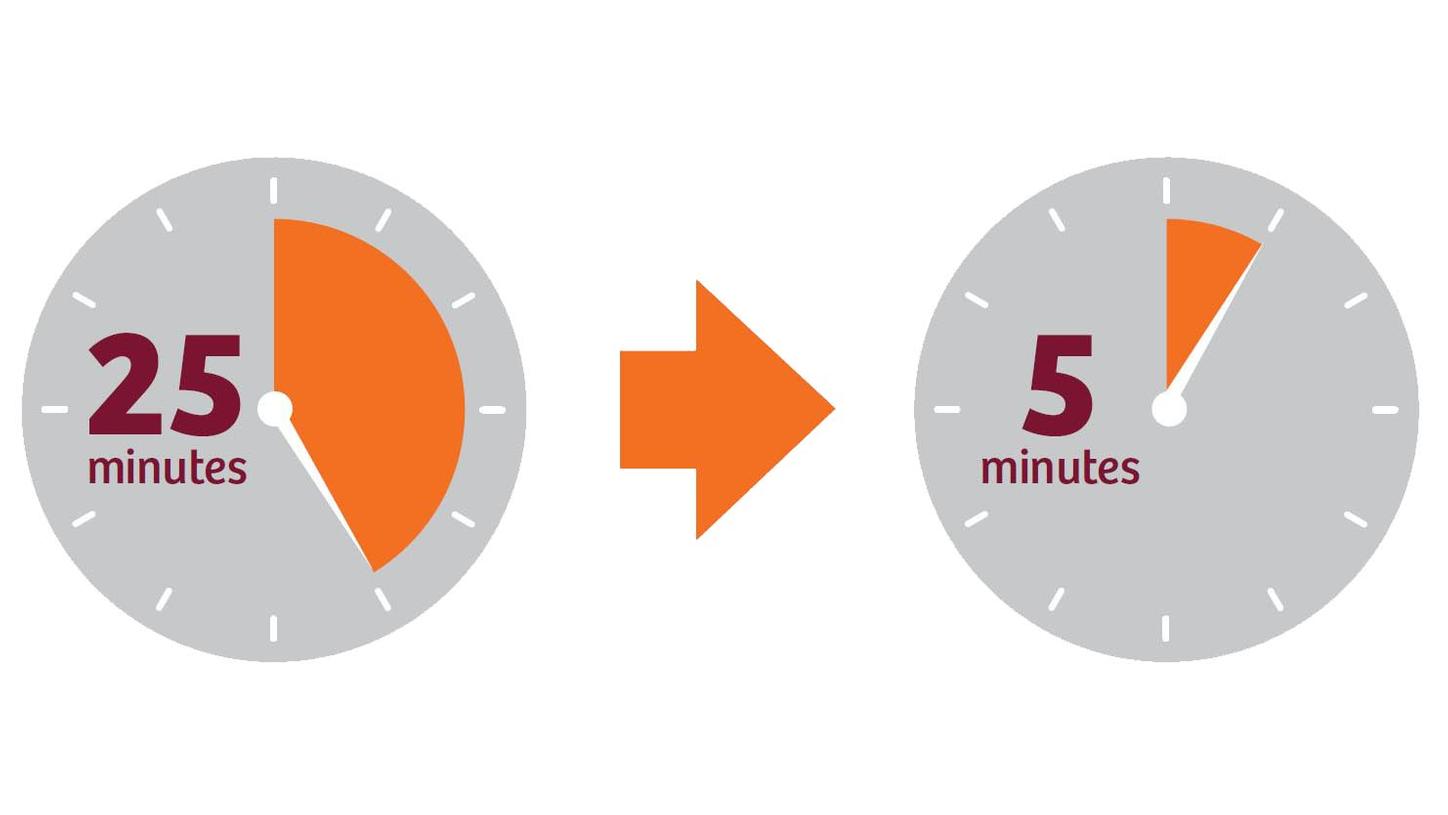
Klinikum Frankfurt Höchst sees time savings of 35%
When implementing Atellica IN, Klinikum Frankfurt Höchst faced the challenge of how to deploy the system over its multi-floor building layout. Siemens Healthineers consultants demonstrated Atellica IN’s built-in ability to adapt to different infrastructure layouts and laboratory settings, and a two-floor setup was installed at the hospital.
The next hurdle was to build laboratory staff confidence in Atellica IN. The staff members who had handled inventory management manually were hesitant to fully trust the automated system. Within two weeks, however, Atellica IN proved its reliability as well as its efficiency advantages. By automating inventory management, the medical center has achieved total time savings of 35%.
“Atellica Inventory Manager centralized everything. We get a total overview of all items in stock and can complete purchase orders at the push of a button.”
Among individual tasks, the time it takes to check inventory before ordering has dropped from 25 minutes to 5 minutes, saving up to 4 hours per week. Placing an order manually used to take approximately 45 minutes several times a week, including manually counting stock inventories at different storage locations, filling in purchase order forms, and sending them by fax.
Costs are lower too. With Atellica IN providing inventory and expiration-date alerts, as well as backorder information, the medical center has nearly eliminated the extra expense and workload associated with emergency orders. Optimizing inventory levels reduces holding costs for excess supplies and waste due to product expiration. The system reduces human error while freeing staff to return to high-value work, which in turn increases job satisfaction and morale.
Ultimately, a lab’s mission is to support high-quality patient care by providing clinicians with fast, accurate test results. Atellica IN supports this mission by ensuring that no supply issues impact turnaround time or staff efficiency.
“With defined minimum stock levels and a consistent order process, Atellica Inventory Manager enables us to consolidate the ordering processes of multiple departments while also customizing for different lab requirements,” Dr. Colhoun says. “Staff found it easy to learn the system, and our highly skilled med techs are delighted to use their time for medical- and lab-related work instead of counting packages and submitting orders. Such efficiencies support the highest quality of patient care.”
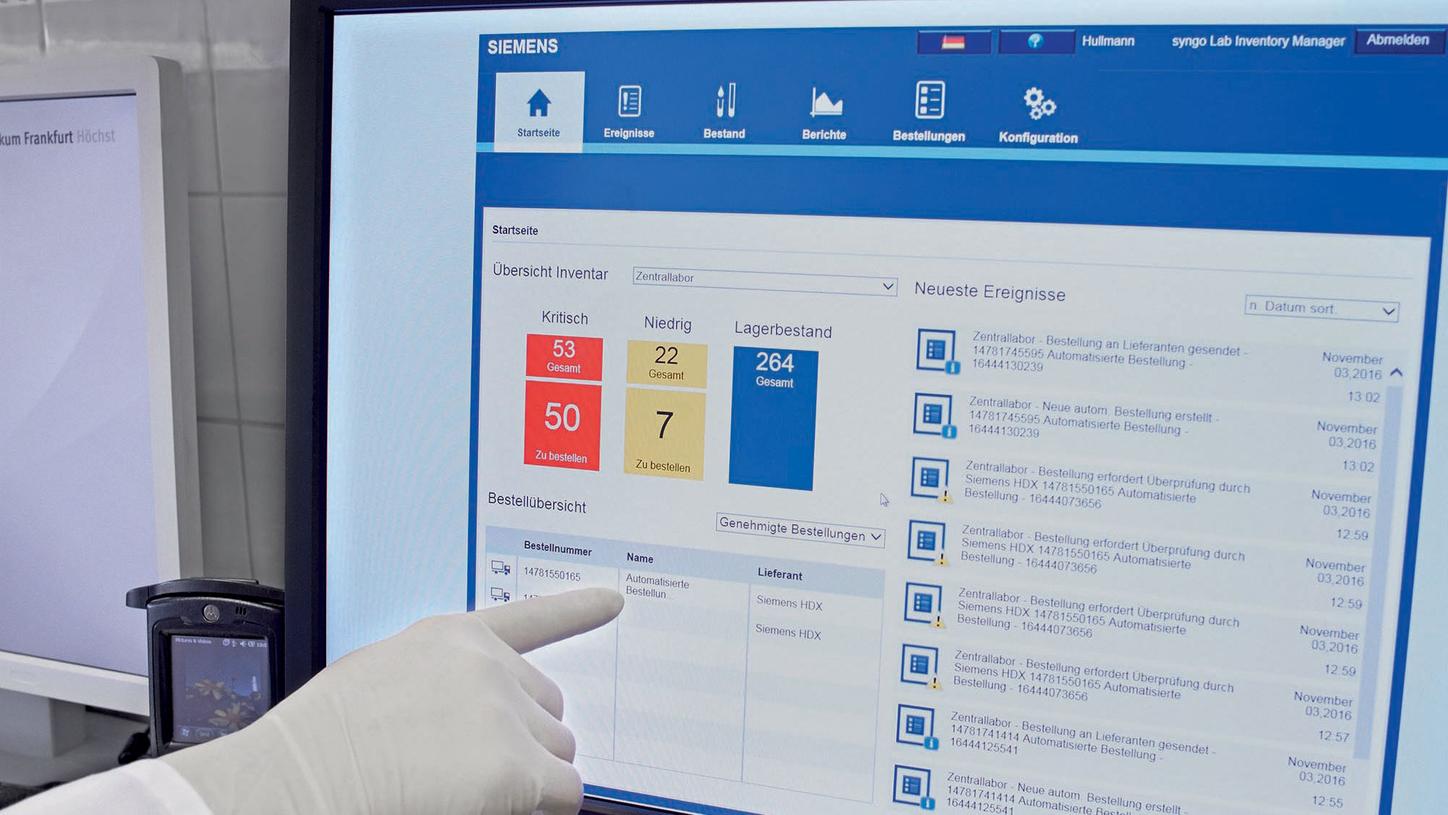
Automated visibility for compliance documentation
The solution also simplifies regulatory compliance. Klinikum Frankfurt Höchst follows RiliBÄK German Medical Association quality guidelines and maintains the highest levels of accreditation. In the past, the medical center documented its inventory management manually. Now, Atellica IN tracks supplies and orders automatically, including delivery date, check-in person, date consumed, expiration, lot, and other factors.
Order data can be printed, emailed, or exported to Excel spreadsheets, and the software can analyze consumption patterns.
“It would be very difficult for us to manually adhere to increasing quality regulations,” Dr. Colhoun says. “Even with stricter requirements, Atellica Inventory Manager’s statistics tool is very useful and accepted for documentation purposes.”
“The biggest benefits to us are improved staff utilization, standardized order processes, and reduction of inventory stocks.”
Forward-thinking institution embraces quality-enhancing efficiencies
Klinikum Frankfurt Höchst has been a forward-thinking Siemens Healthineers customer since 2006. The hospital stays up to date on instrument and assay advances and enhances its administrative processes to improve outcomes. Leveraging Atellica IN to track, manage, and order consumables and analyze laboratory inventory data, Klinikum Frankfurt Höchst improved resource utilization, cut costs, saved labor time, improved quality, and gained end-to-end visibility for easier regulatory compliance.
“The biggest benefits to us are improved staff utilization, standardized order processes, and reduction of inventory stocks,” Dr. Colhoun says. “Atellica Inventory Manager has transformed our inventory-management process. We consider it essential to the optimal efficiency of a modern healthcare institution.”