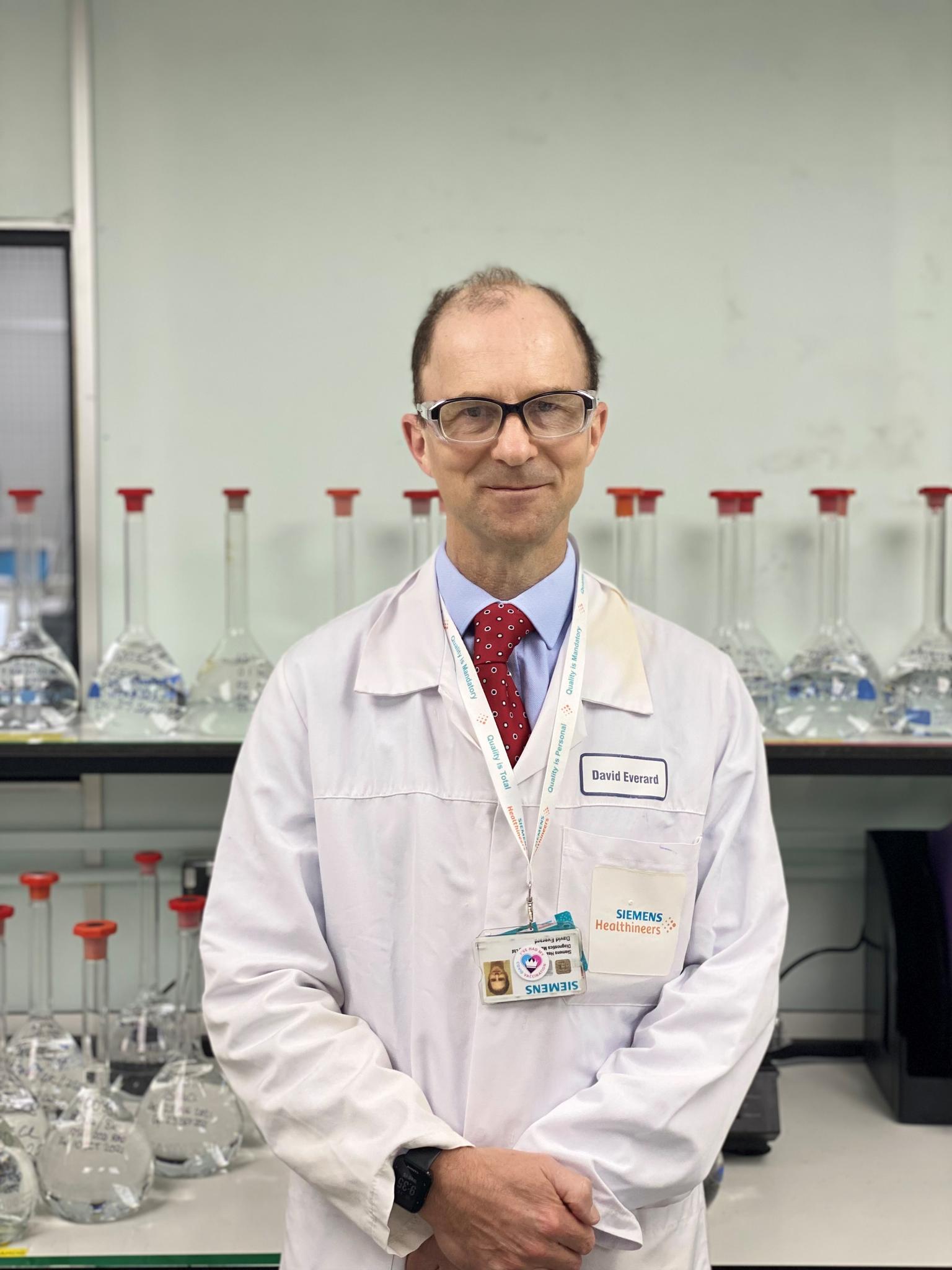
Sudbury team learns to produce new raw material and avoids production shut down.
I am David Everard, and I am a Laboratory Coordinator at Siemens Healthineers Sudbury. In March 2020, the Sudbury Quality Control team faced a critical risk to production: One of our raw material suppliers experienced unforeseen manufacturing issues and suddenly notified Siemens Healthineers that they could not provide us with LDH (Lactate Dehydrogenase) for approximately six months.
Our QC team uses LDH to assign Lactate values to every 200 Cal pouch batch. An elevated Lactate result can be an indicator for Sepsis (among other diagnoses), so accuracy is essential. Furthermore, without 200 Cal, we would be unable to make cartridges for our RAPIDPoint® 500e or RAPIDLab® 1200 blood gas systems – which are critical in the fight against COVID-19.
Our lab stock of LDH was quickly being used due to the ramp up of 200 Cal batches, and a shortage from our supplier would have resulted in our inability to test the batches for four months. Given customer expectations, and of course the increased demand for cartridges due to the pandemic, we could not afford a shutdown in production.
While our team worked with the supplier to see if they could get us the material sooner, Dan Cook and myself rapidly researched and developed a method to manufacture our own LDH material in-house.
With assistance from Merck Technical Operations team, we obtained the additional chemicals required, ran the calculations to obtain the necessary enzyme activities, and formulated the required pH and BSA (bovine serum albumin) buffer solutions needed.
Once the new LDH material was formulated, we performed a pFMEA, which is a process failure mode effects analysis. Chris Parker assisted in approving the pFMEA out of his working day with the risk assessment, so that we did not delay the process. We executed a method validation and new method instructions along with a TMD (Temporary Method Deviation). This was a great team effort with prompt assistance from multiple teams, including Procurement, Validation, Quality, and QC.
The new material worked perfectly and the risk to the business was averted! There was no delay in releasing 200 Cal to the cartridge line and no break in cartridge production for our blood gas analysers – which allowed us to deliver on customer commitments.
To further mitigate future risks, we have increased our lab safety stocks and are working closely with our suppliers on their notifications, lead times and alternate sources for materials.