Lab Performance Directly Affects Profit
In the past, labs were considered a revenue center, but regulatory changes are slowly reducing that profit. It has become clear to executive management and lab management alike that it is imperative to improve lab quality and productivity. Doing so will continue have a direct positive effect on reimbursements, reputation, and revenue.
In an emergency department (ED), a hospital bed is a valuable and limited resource. So the faster a clinician receives a quality result, the better the patient care and the sooner discharge or admission can occur, thereby increasing the opportunity to treat more patients in the same space. For example, if a 20-bed ED is able to treat one more patient per bed per day, an additional 7300 patients per year could be served. According to a study by the American College of Emergency Physicians, patients with commercial insurance contribute between $70 and $1773 per hour toward profit, therefore increasing patient volume as outlined in the above example would produce significant financial benefits to the institution.
More patient volume is only one financial benefit of improved lab performance. Better performance also drives revenue through higher levels of reimbursement, reduced risk of penalties, increased patient satisfaction, and the ability to acquire specialized credentials such as chest pain certification, all of which add to the overall profitability of the hospital.
Chest pain is among the most common complaints in the ED, accounting for an estimated 15 to 20 million patient visits per year in Europe and the United States. Decreasing turnaround time (TAT) for cardiac markers such as troponin helps physicians to accurately and more quickly identify or exclude a diagnosis of acute myocardial infarction so they can determine the appropriate course of action. Since a significant percentage of patients with chest pain do not need to be admitted, accurate and timely exclusion is a benefit to both the patient and the hospital.
Conversely, an early and correct diagnosis reduces the chance of incorrectly discharging a patient who would end up being readmitted. Many regulations and directives are focused on improving quality of care, and hospitals may be penalized for excessive readmissions. In the U.S., Medicare has levied penalties called Readmissions Adjustment Factor against thousands of hospitals, with the maximum punishment being 3% reduction in payments for every patient over the following year.
Instrument speed and assay sensitivity are just a small part of the total time to reportable result. An analysis of the workflow from “vein to brain,” or blood draw to results to the physician, can clearly demonstrate that most delays can be found in inefficient processes before and after the analysis—not just within the lab, but throughout the hospital. Resolving these issues can significantly benefit the health of the patient and financial health of the hospital.
When Is the Right Time to Engage a Consultant?
Consultants can provide insight, guidance, and cost justification for everything from simpler projects, such as refining floor plans or identifying an optimal testing menu, to more complex plans, such as implementing total (track-based) lab automation systems or designing a brand-new lab.
Ideally, a workflow consultation should be performed whenever you plan to:
- Improve the efficiency and productivity of your current workflow
- Transition to lab automation for the first time
- Move from legacy automation to a new solution
- Consolidate specialty labs into the core lab
- Integrate labs as part of an acquisition
- Construct a new lab
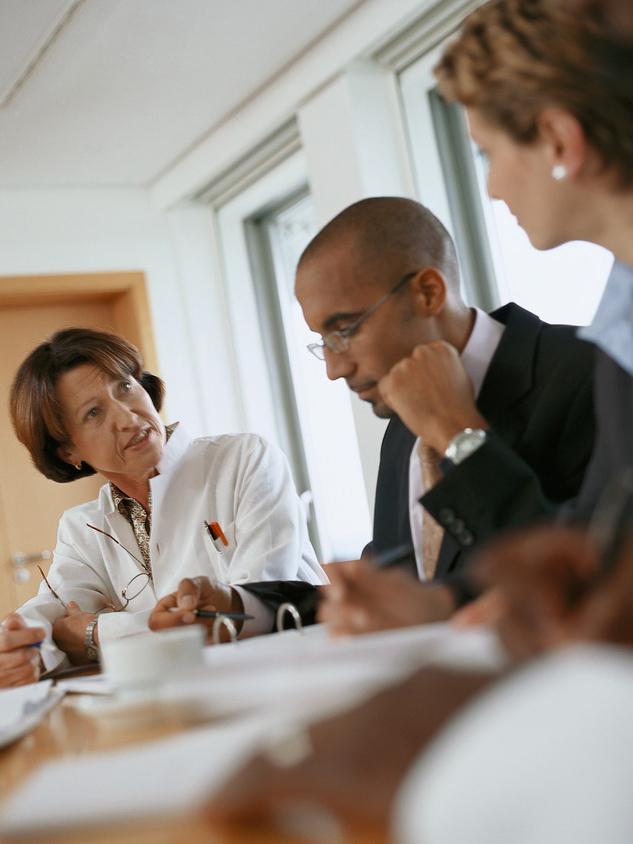
What to look for in a workflow consultant
Expertise
Do they have experience across a broad range of labs and projects?
Education
Do they have Lean healthcare certification, Six Sigma green or black belts, informatics training, or IVD diagnostic laboratory expertise?
Credibility
How did the consultant’s analyses and recommendations help other customers to achieve their goals? Can they demonstrate success serving other labs with similar projects?
Reputation
What do their customers say about working with them?
Commitment
Will they remain available through implementation and go-live? Do they provide follow-up analysis, adjustments, and re-evaluations?
“Our analysis includes not only highly focused observation, but also in-depth analysis of an incredible amount of data”
What to Expect from a Consultation
To gain a holistic understanding of your operations, a workflow consultant should scrutinize every moment in the “life of the tube.”
Pre-analytical Processes
Up to 60% of the total TAT occurs before the tube even reaches an analyzer. Even the fastest-performing systems won’t be able to make up time if the prior workflow is slow and inefficient.
“Often, we can make some substantial adjustments in the pre-analytical stage, where many labs are losing valuable time,” says Ms. Yost. “Sometimes even surprisingly simple changes can make a drastic improvement, such as switching to hands-free bar-code scanners. While this may seem to save only a moment’s time compared to picking up a handheld scanner from the bench, multiplied by thousands of tubes per day, the motion and time savings can be significant.”
Analytical Systems
Clinical chemistry generally accounts for about 50% of the overall volume of diagnostic testing. However, the chemistry area is typically located in the back of the lab due to space limitations. This frequently creates extra motion, transportation, and batching that can be addressed through process re-engineering or floor-plan redesign.
A lab’s testing menu also plays a key role in overall performance, cost, and value to physicians. A consultant should look at the current mix of tests and evaluate the respective volume, cost, reimbursement, and TAT implications of tests performed in-house versus send-outs. This helps identify the ideal menu and the right mix of analyzers to meet the lab’s needs.
Post-analytical Processes
Your consultant will evaluate the impact of follow-up analysis such as repeat, reflex, and sort-out testing, considering your current storage capacity, work space, sample handling, and disposal methods.
Add-on testing is often the biggest drain on post-analytical productivity. “Two to six hours per day can be wasted scouring through archived tubes by hand,” says Sue Yost. “We often recommend solutions that include refrigerated storage with automated retrieval to lessen demands on staff, reduce biohazard exposure, and regain a significant amount of lost time and productivity.”
Floor-plan Design
When analyzing floor plans, consultants use a spaghetti diagram to reveal poor space utilization and unnecessary movement of tubes, staff, consumables, and information. After assessment, efficiency can be measurably improved simply by changing the order of steps, eliminating rework steps, or bringing supplies and equipment closer together. “By changing maintenance and quality control procedures for one customer, we eliminated over 1000 trips to the refrigerator and more than 4 miles of walking annually,” recalls Sue Yost.
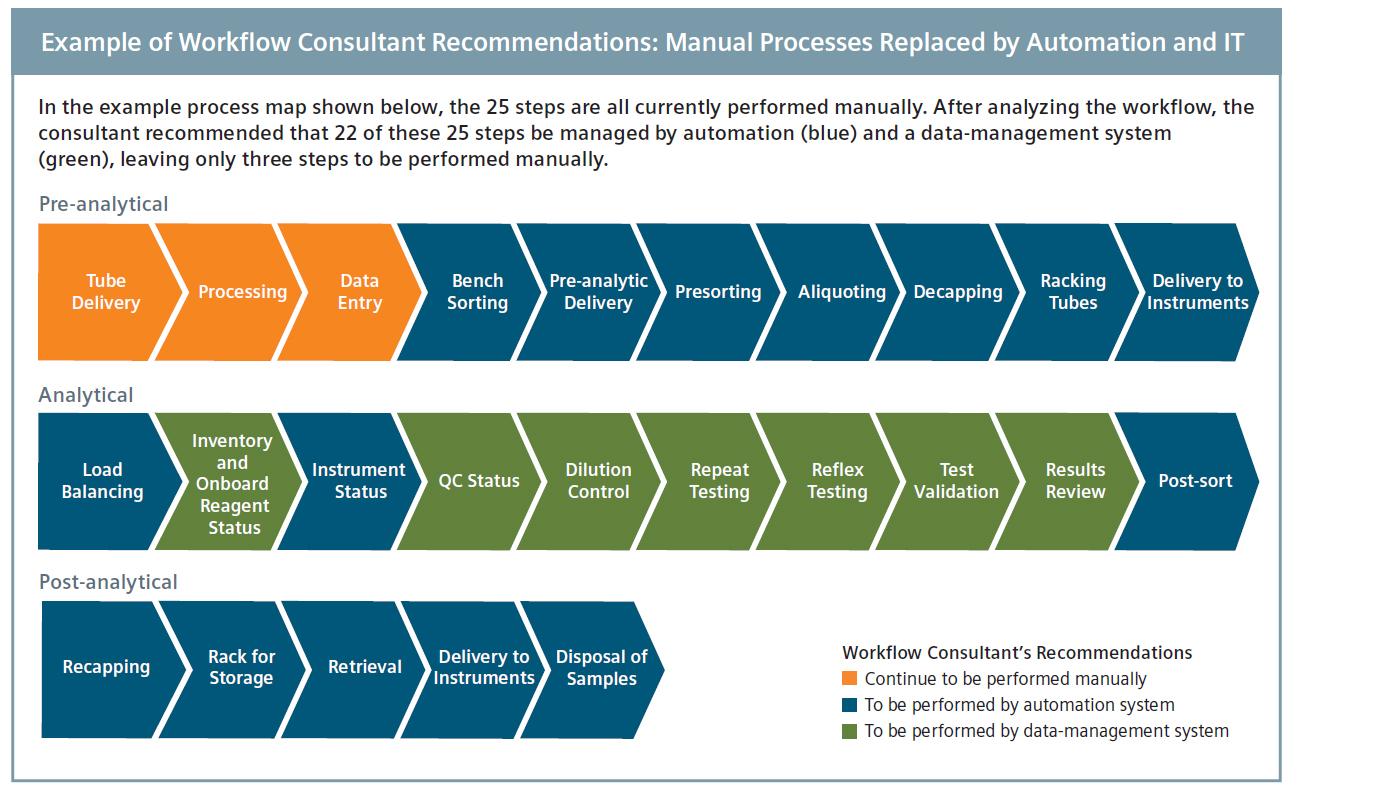
Example of Workflow Consultant Recommendations: Manual Processes Replaced by Automation and IT
Workflow Assessment
A workflow assessment typically follows a three-step process:
Step 1. Goals: What do you want to accomplish?
Consultants typically begin by reviewing the lab’s current operations and discussing what must be accomplished to meet current and future needs.
“The first thing we ask the lab management is what they think is working well and what is not,” says Ms. Yost. “Then we get into the specifics. Are they seeking specialty certification? How do they manage add-on test requests? Do they autoverify patient results? Is blood draw tracked electronically?”
Step 2. Current state analysis: How is your lab working today?
A lab assessment is very hands-on but also extremely data-driven. “Our analysis includes not only highly focused observation, but also in-depth analysis of an incredible amount of data,” says Sue Yost. “We measure key performance indicators (KPIs) throughout the lab so we know exactly what is going on and what benefits our customers can expect to see from our recommendations.”
Many tools and principles come into play here, with some of the most commonly used highlighted in the Toolbox below. This period of evaluation can vary in duration and scope, depending on the lab’s needs and goals and the consultant’s judgment.
Conclusions should be built upon hard numbers. Your consultant will analyze several days’ worth of peak and off-peak log, lab information system (LIS), and middleware data, followed by on-site observational analysis, and then correlate the data with what is actually happening in the laboratory. This process will identify areas of need and will serve as the foundation for the consultant’s recommendations.
“Typically, we’ll spend an entire day or more watching people and processes while taking extensive notes,” says Ms. Yost. “We create value stream maps, draw every step that we observe, and identify pain points that the customer may not even know exist.”
The evaluation may include several focused analyses:
Production analysis: Measures tubes and tests per hour in each analyzer and module, paying careful attention to distribution within module and analyzer groups, load balance, and how samples are being processed (e.g., batch size, front-loading, etc.)
Utilization analysis: Focuses on the theoretical and effective capacity of each analyzer and module to determine if a lab may need to add equipment to support expected growth and meet service level agreements with its clients.
TAT analysis: Looks at routine and STAT samples and measures mean, standard deviation, 95th percentiles, and other parameters. TAT can be measured holistically across a larger area such as pre-analytical, or specifically to an analyzer, analyzer group, module, or test. This level of scrutiny helps uncover the true causes of delays.
Error analysis: Studies errors and information messages identified by the automation system and attached modules. Viewed in isolation, these may seem minor, but very high numbers or patterns appearing across days can highlight sample-handling issues that reflect on the human-machine interface. This is particularly helpful when comparing across all three shifts in a 24x7 operation.
Step 3. Conclusions: Identifying problems and recommending holistic solutions for an improved future state.
Experienced and well-trained consultants are extremely effective at finding problems and proposing what needs to be done to meet your lab’s goals. The solution should map directly back to your original goals, and forecasted performance data should support your stated objectives.
In the end, your consultant will provide one or more recommendations based on your lab’s current state and tailored specifically to your goals, budget, and staffing situation. Recommendations may include a mix of several changes, including processes, instruments, workflow, menu, IT, and automation, each contributing to the overall holistic solution. Some fixes can be surprisingly simple, and others will be more significant endeavors.
The Workflow Consultant’s Toolbox
Consultants use a variety of process-improvement methodologies and tools, including:
Six Sigma
A measurement-driven approach to quality and process improvement that identifies and removes the causes of lab errors and minimizes variability in daily processes.
Lean Healthcare
A proven methodology for standardizing and improving processes that reduces wasteful activities.
Value Stream Maps
A tool for visualizing the current-state process and designing for a future state. The maps identify steps that do and do not add value, helping to eliminate what is not needed.
LIS and Middleware Data
Provides data-driven insight into current-state TAT, bottlenecks, and inefficiencies.
Spaghetti Diagrams
Useful for re-engineering floor plans, these maps track movements of people, samples, and information to identify excessive movement and transportation and poor space utilization.
Simulation Analysis
Models how proposed solutions will perform and allows you to compare options and quantify benefits of proposed solutions.
Two- and Three-dimensional Modeling
Detailed floor plans and walk-through simulations that provide a clear vision of the proposed solution.
Rapid Improvement Events
Extremely focused action plans for addressing a specific process.

Examples of simple but effective fixes:
- Replace warning buzzers with flashing lights: Busy technicians may tune out the noise, but a light is readily noticeable without adding to the cacophony of the lab.
- Relocate obstacles: Benches, doors, cabinets, or wires often can form an unnecessary barrier between work areas. A simple move can be enough to ease congestion or reduce steps.
- Display pending results: A large wall-mounted monitor gives everyone clear insight into the status of the lab and is incredibly valuable for managing operations.
- Switch to plasma instead of serum: Serum clots in the tube; plasma does not. Many commonly used medications interfere with the clotting process, creating bad serum samples for analysis.
More complex initiatives that yield significant results:
- First-time move to automation: Many labs don’t think they need or can justify the budget for automation. But the return on investment (ROI) can be calculated by your consultant to validate your decision.
- Upgrading to a new track or extending an existing one: Flexible and open systems support multiple disciplines and a wide range of instruments and modules to grow and evolve with your lab’s needs.
- Tearing down walls: Big, open floor plans are best and promote efficiencies. This may involve significant changes to lab space.
“One of the things I’m most proud of is how many customers will say to me, ‘I can’t believe how much you saw in my lab in two days, and how much improvement we gained,’” says Ms. Yost. “To me, that’s the biggest compliment, because it means that I’m paying attention to my customer’s needs and providing a very valuable service.”
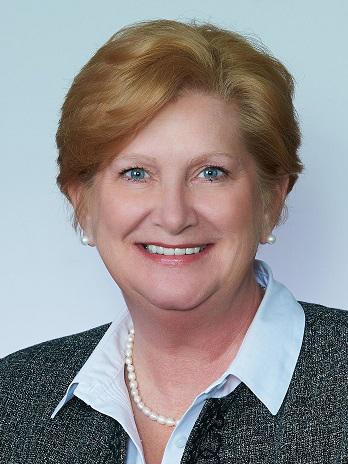
Susan Yost
Automation Manager
Healthcare Consulting Solutions
Siemens Healthcare Laboratory Diagnostics
Susan Yost is an automation manager with Siemens Healthcare Consulting Solutions. Prior to joining Siemens in 2005, she worked for 27 years in clinical laboratories. She is Six Sigma- and Lean-certified in healthcare operational assessments and floor-plan design from the University of Michigan.