Home
- Press center
- Press features
- The digital lighthouse in Forchheim: The High Energy Photonics (HEP) Center
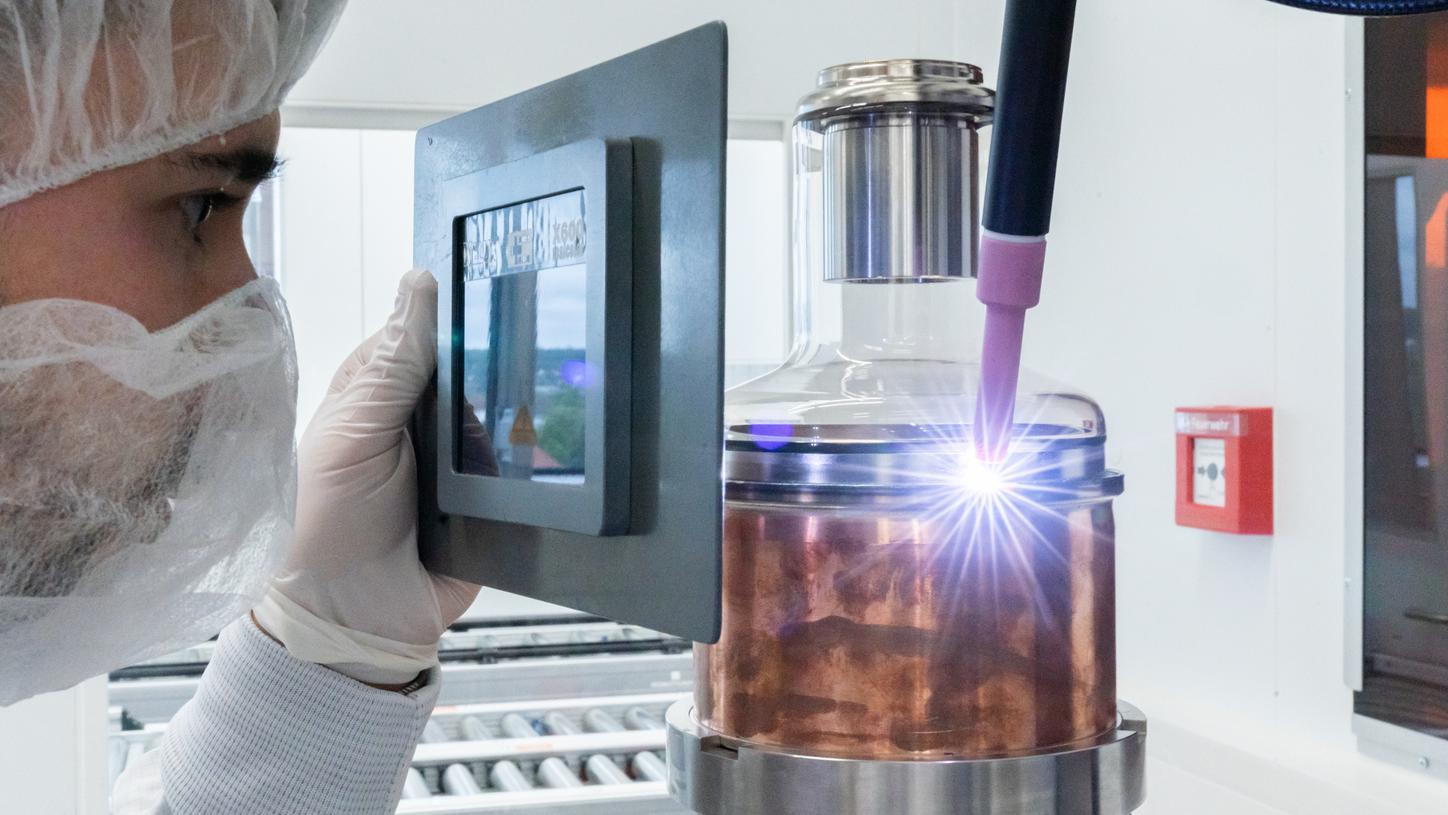
The digital lighthouse in Forchheim: The High Energy Photonics (HEP) Center
Not for publication in the USA
The HEP Center Forchheim, a Siemens Healthineers facility, is at the forefront of technological innovation in the medical imaging field. As a state-of-the-art production facility of Siemens Healthineers, it is the birthplace of high-performance X-ray tubes and generators for imaging systems. It stands out by a complete end-to-end digitization and automation approach, integrating production, development, and office areas. The HEP Center, which consolidates two existing factories in Erlangen, was initiated in 2019.
With the integration of advanced technologies such as flexible cobot systems, robotics, and sensors, the center is transitioning from traditional manufacturing to automation and digitalization. The HEP Center Forchheim exemplifies Siemens Healthineers' commitment to transforming healthcare through cutting-edge technology and a skilled workforce dedicated to lifelong learning.
Flight into the future
Creation of a "Transparent Factory"
The facility's embrace of digital tools and automation has led to the creation of a "transparent factory" where everything is interconnected digitally—from shop floors to equipment to logistical processes, including the digital twin of the building. The digital transformation at the HEP Center aims to enhance work performance, minimize risks, and ensure transparency of knowledge. Here are some examples of how this is achieved:
- Digitalization of Data: The HEP Center focuses on transforming, generating, processing, and connecting digital data to enhance the value added by production and business processes. This approach is aimed at improving the input-output behavior of these processes.
- Automation: The center is actively replacing existing hardware or introducing new hardware to automate at least one manual step in every process. This shift towards automation is a critical component of the digital transformation strategy.
- Digital Shopfloor and Visualization: The HEP Center employs digital tools such as Digital Shopfloor Applications (DSA) and Manufacturing Execution Systems (MES) to visualize Key Performance Indicators (KPIs) and enhance decision-making processes. Advanced planning and scheduling (APS) tools are used for detailed planning.
- Dynamic Capacity Design: In production planning, the HEP Center has achieved a 15% area saving in the High Voltage Conditioning area by optimizing shift balancing. This dynamic capacity design is part of the center's commitment to efficiency and flexibility.
- Smart Factory Integration: The HEP Center is being developed as a fully integrated solution for a Smart Factory, which will be part of the Siemens Healthineers Campus Forchheim. This integration will bring together all necessary disciplines—production, R&D, and business administration—to produce components for X-ray machines in a unique technological environment.
Digital twins optimize products and processes
The center leverages next-level data science and simulation capabilities to create digital twins of products, production, and performance. Digital twins serve as a cornerstone for optimizing products and processes. This model creates a virtual replica of reality, integrating complex information from various sources. It enables the identification of errors before they occur, prevention of downtime, visualized collaboration, real-time insights, a fully digital development process, and predictive intelligence, which means the ability to recognize patterns and forecast events based on statistical analyses.
Promoting Human-Machine Collaboration
This environment fosters a culture of continuous learning and collaboration between humans and machines, each contributing their strengths to enhance productivity and innovation. A special program for employees supports cultural change and skill development, ensuring that the workforce is prepared to succeed in an increasingly digital and automated environment.
Image Gallery
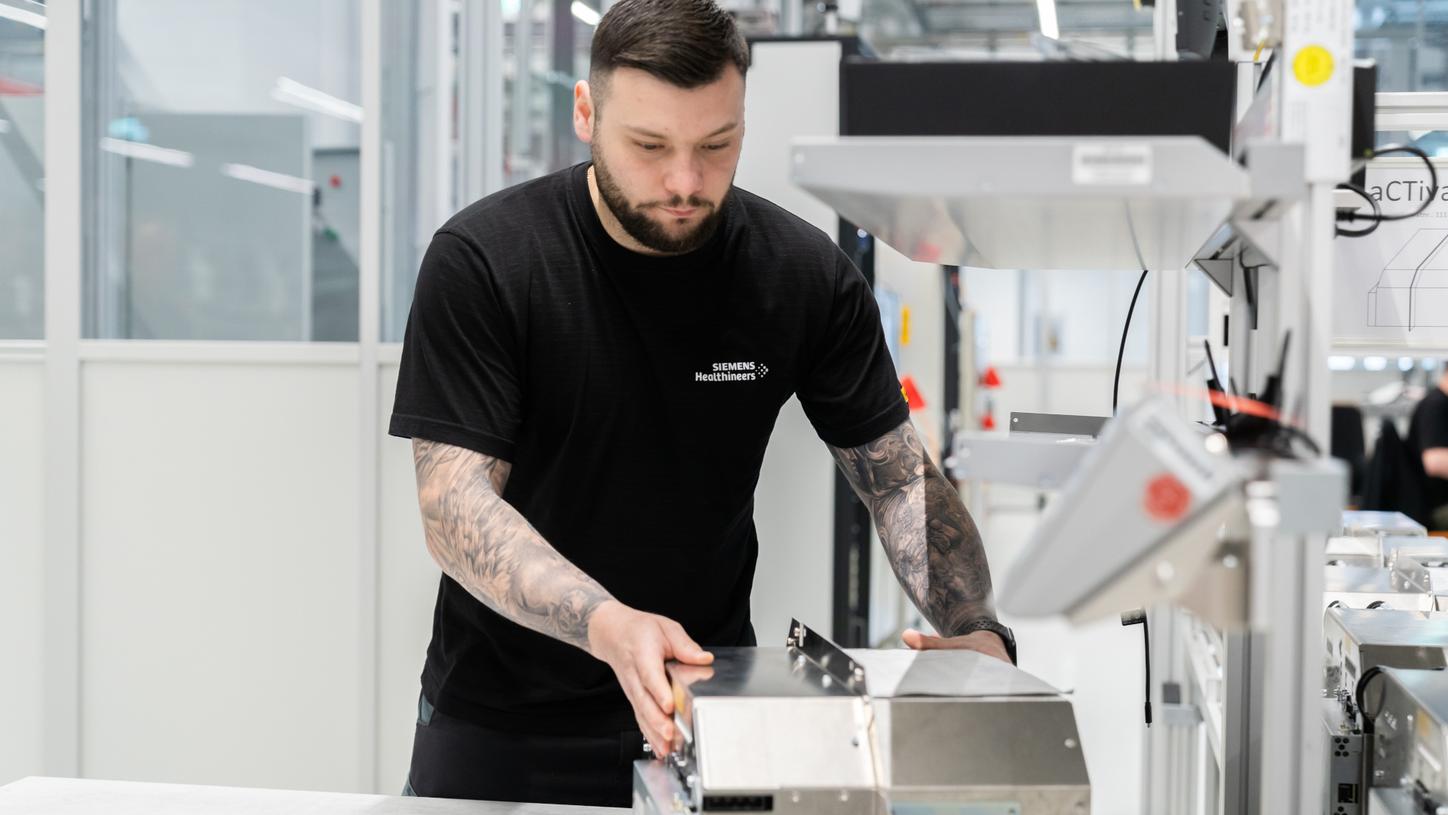
Assembly of housing parts for the high-voltage supply of X-ray tube assemblies.
Download image
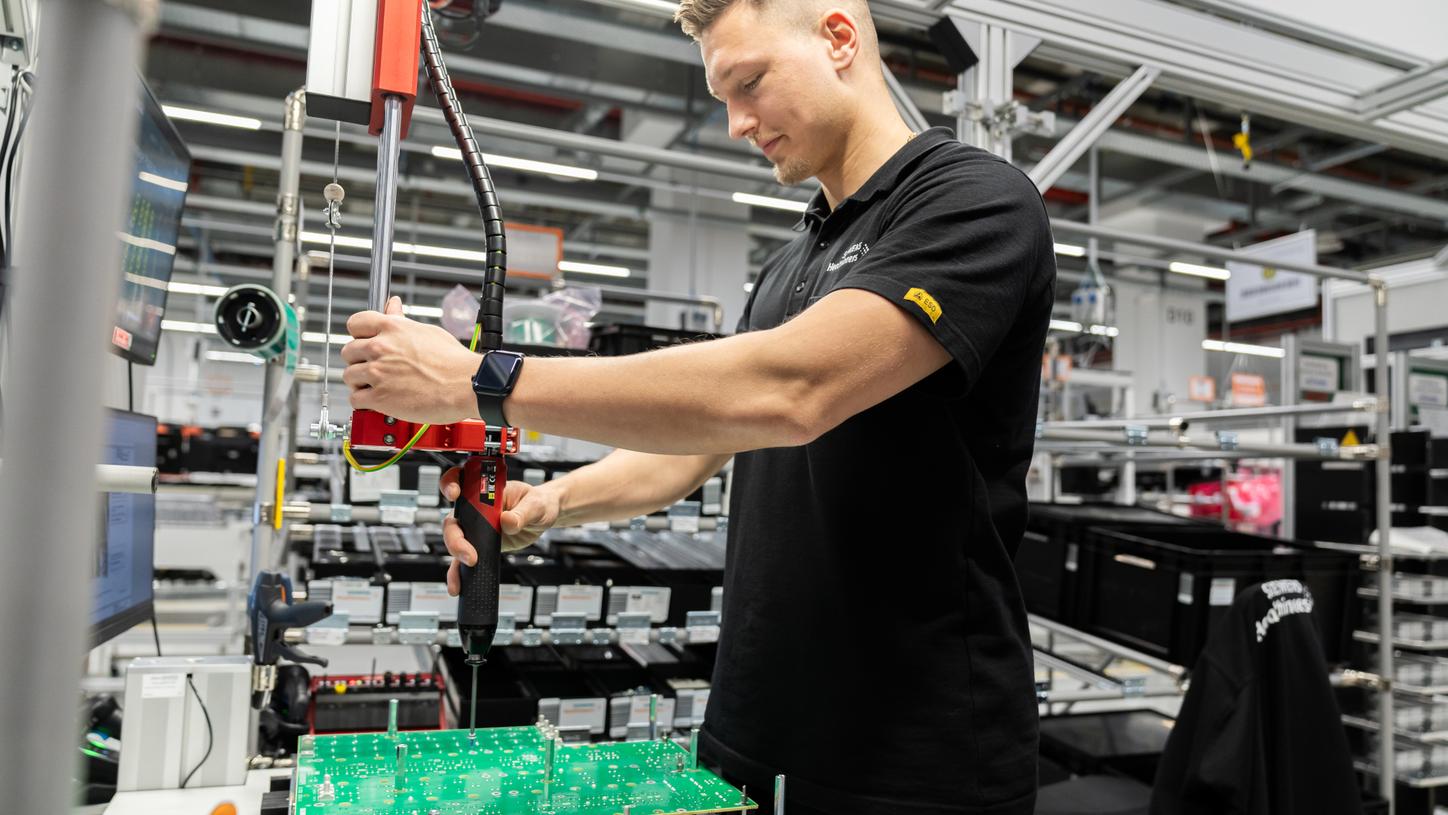
Digitally guided assembly of power supplies for X-ray tube assemblies.
Download image
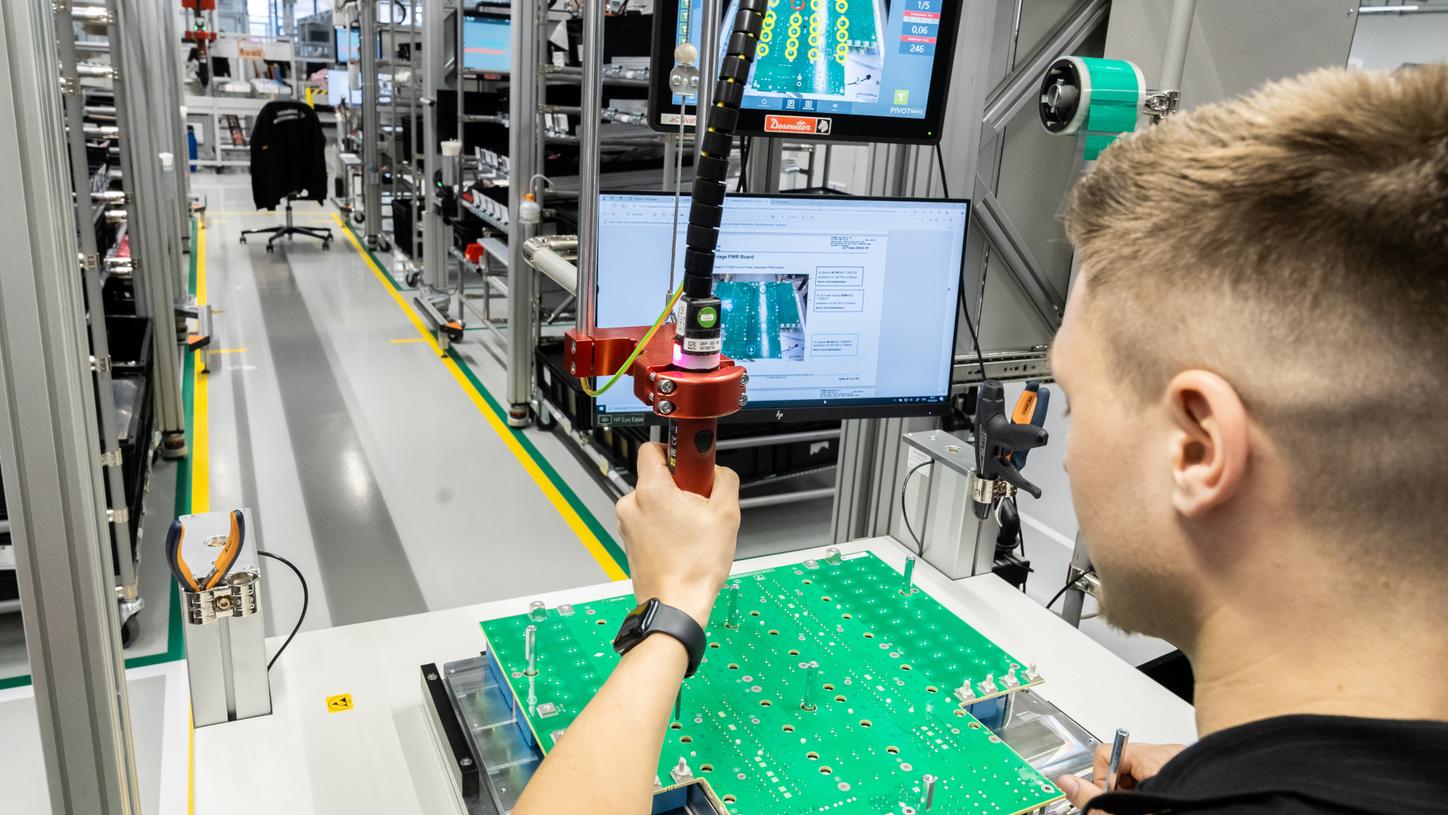
Digitally guided assembly of power supplies for X-ray tube assemblies.
Download image
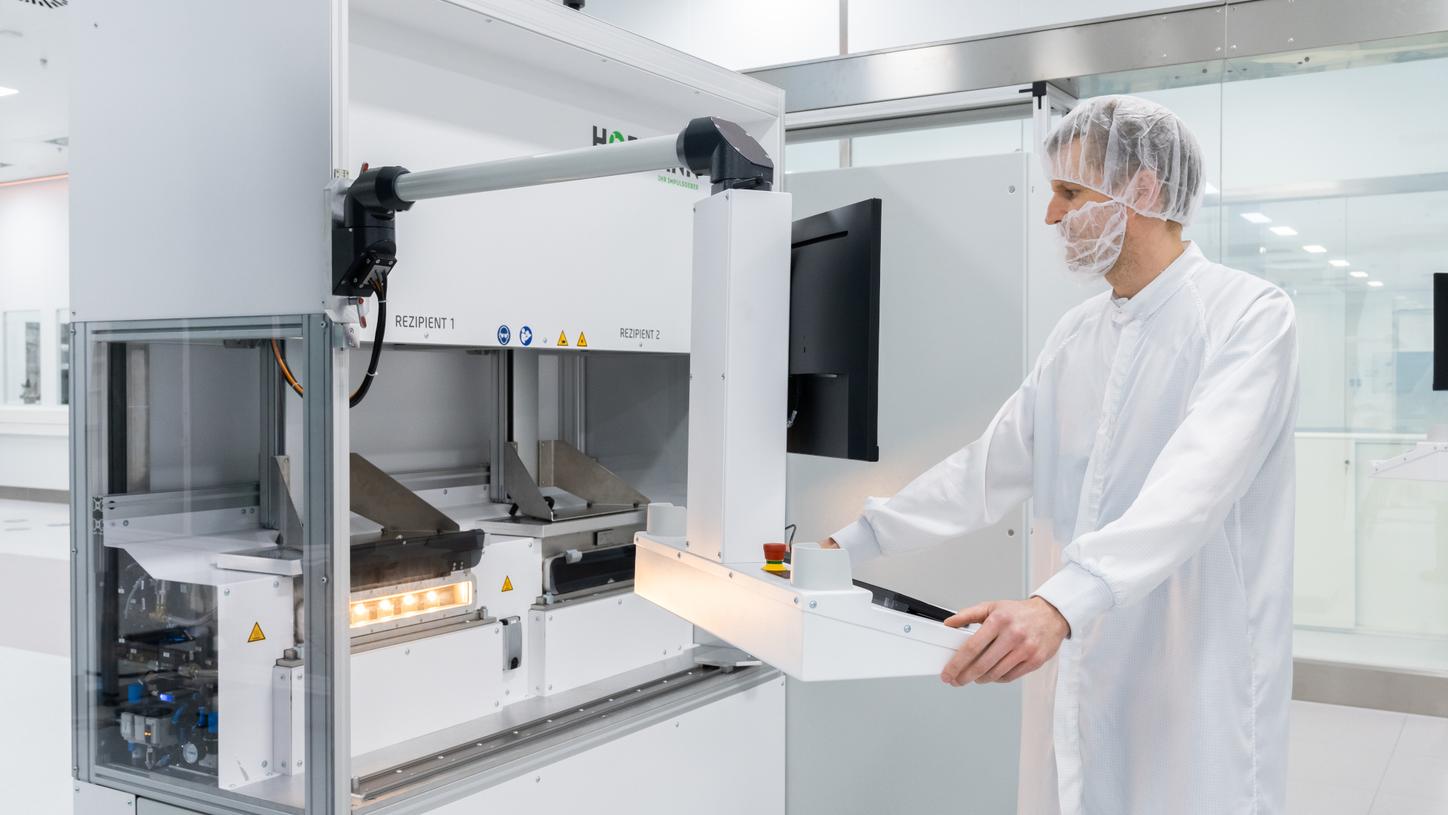
High temperature process of components for X-ray tubes in cleanroom.
Download image
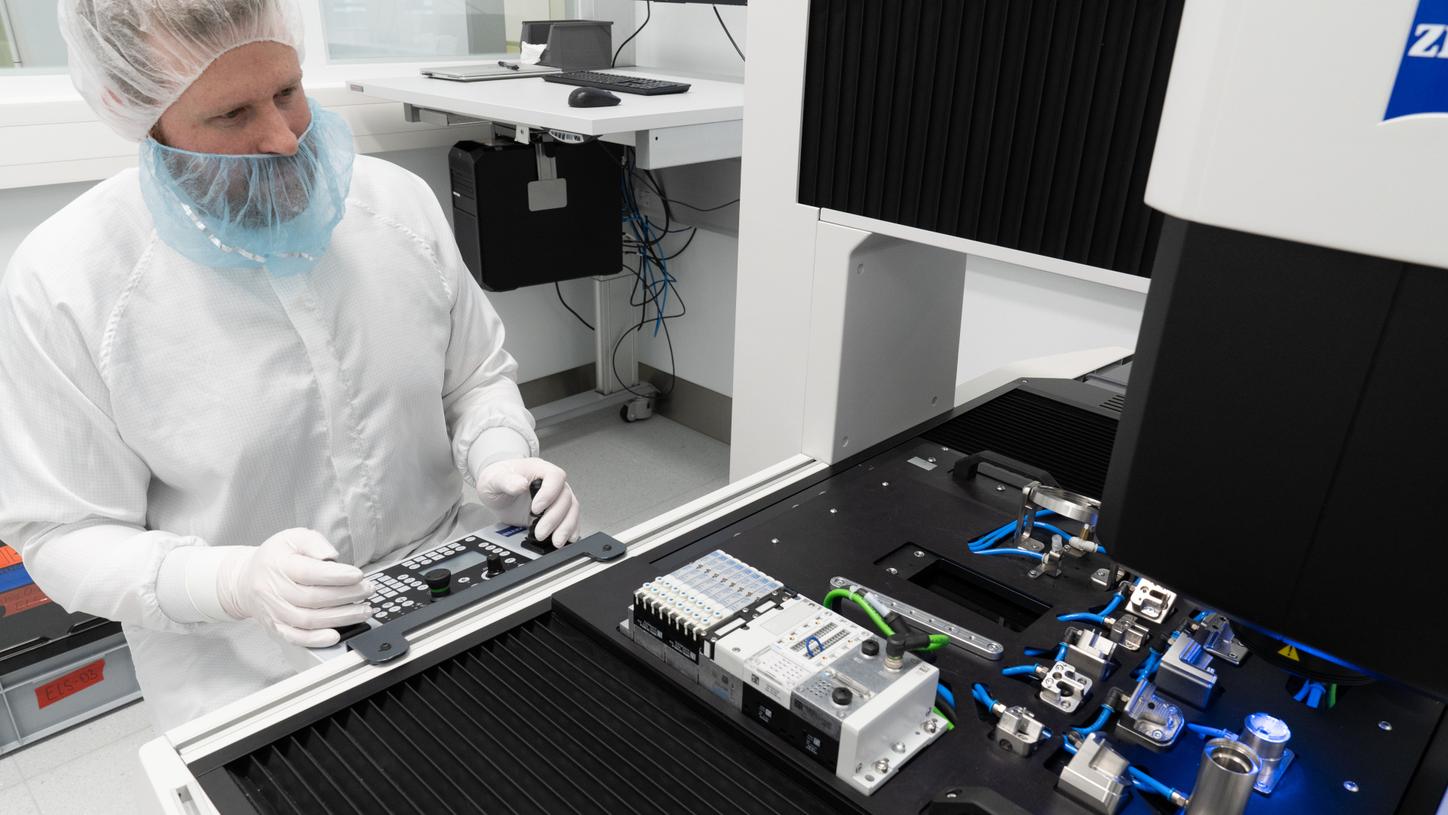
Fully automatic measurement of components of X-ray tubes under clean room conditions.
Download image
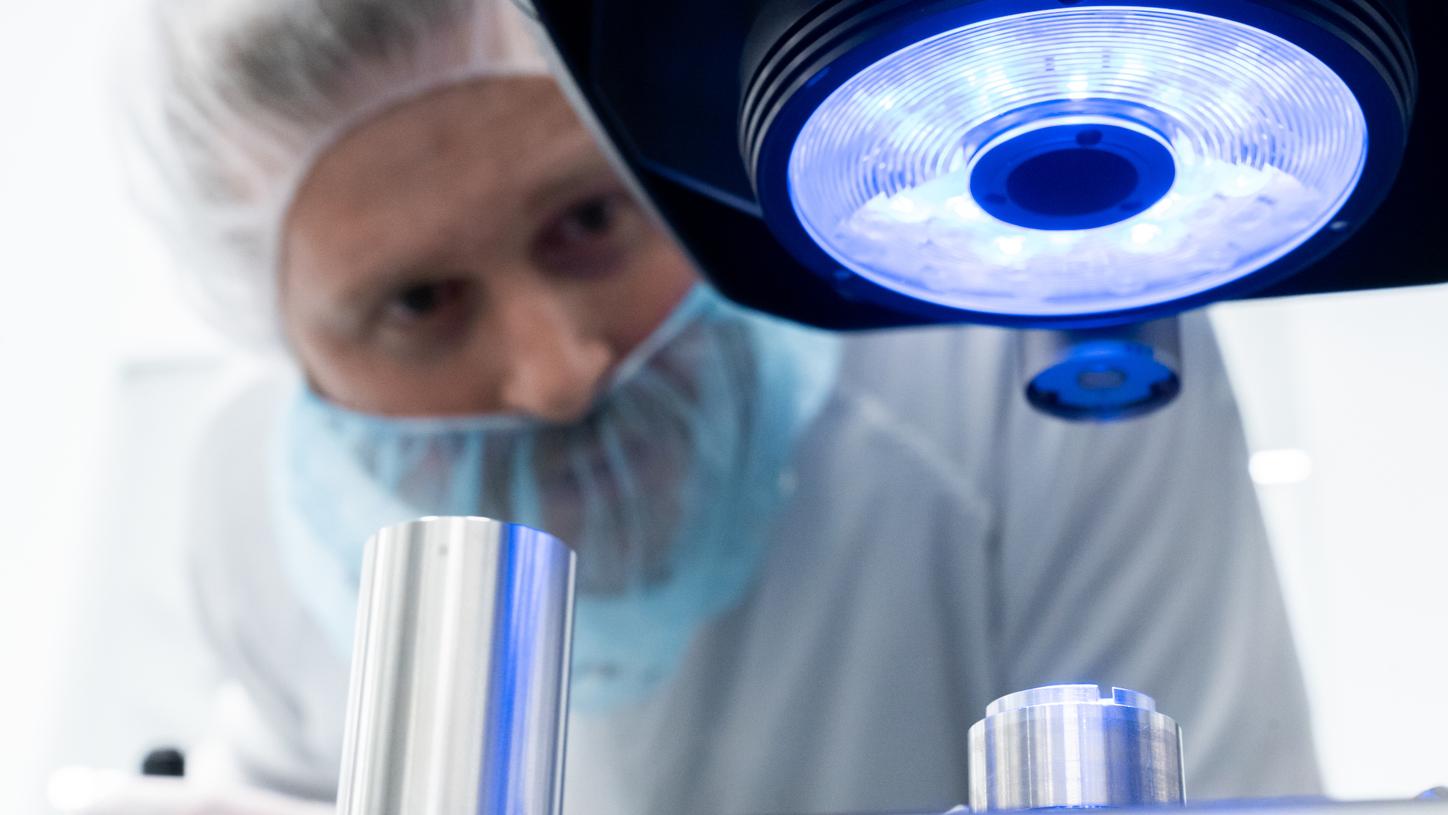
Calibration of high-precision measurement for components of X-ray tubes components in the clean room.
Download image
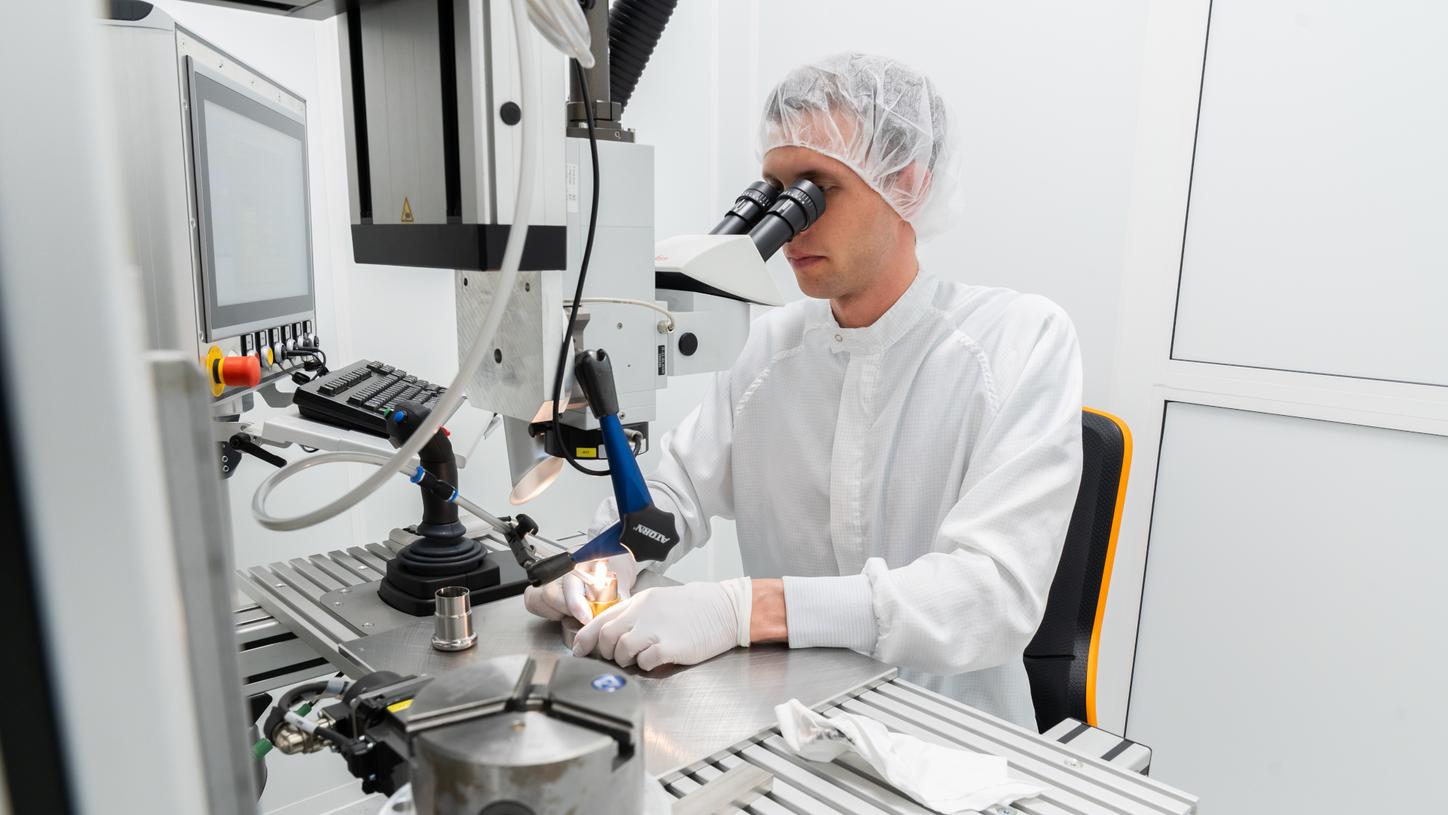
Laser welding of components of X-ray tubes under the microscope in the clean room.
Download image
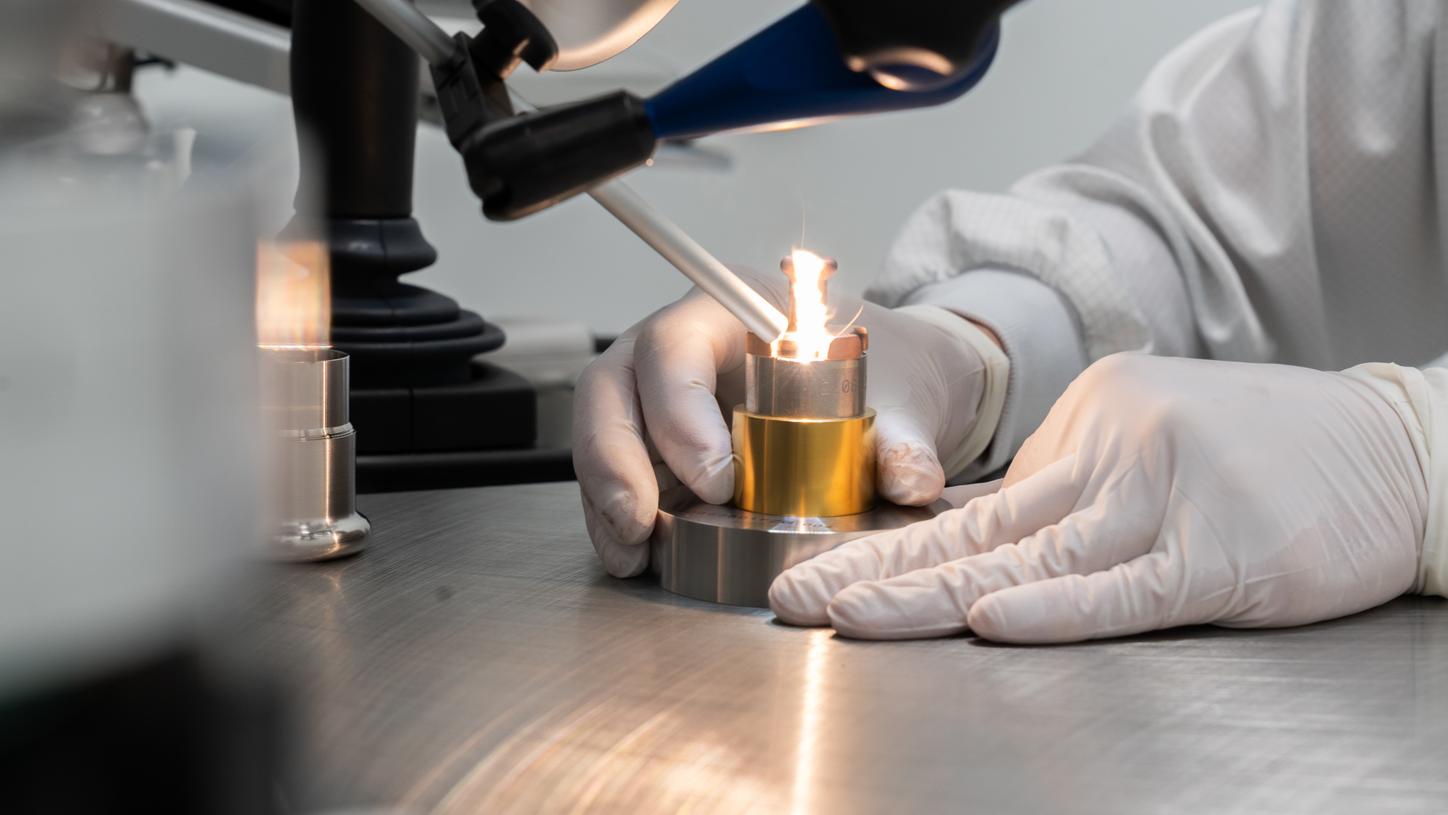
Laser welding of components of X-ray tubes under the microscope in the clean room.
Download image
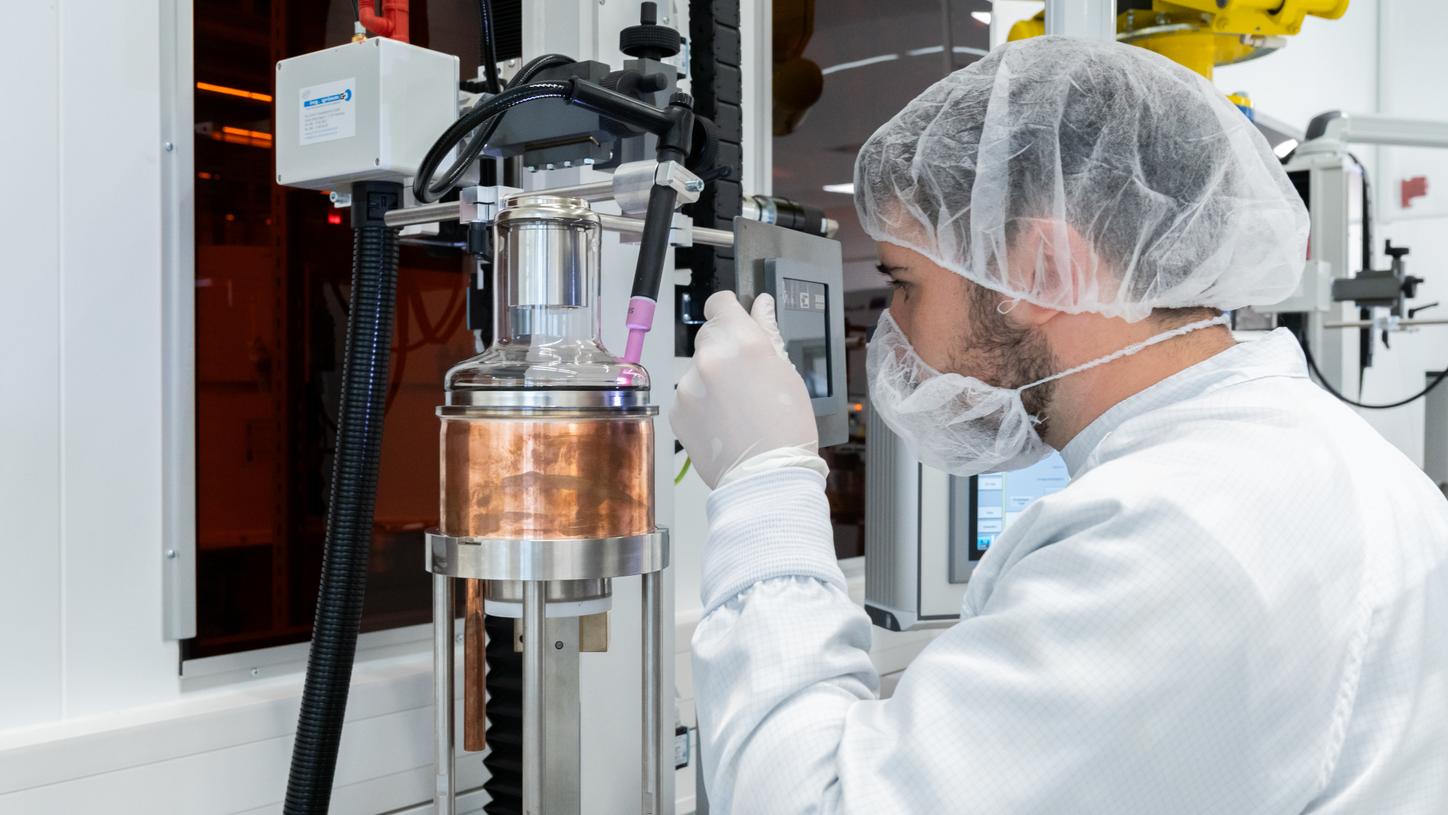
Welding on metal-glass X-ray tubes under clean room conditions.
Download image
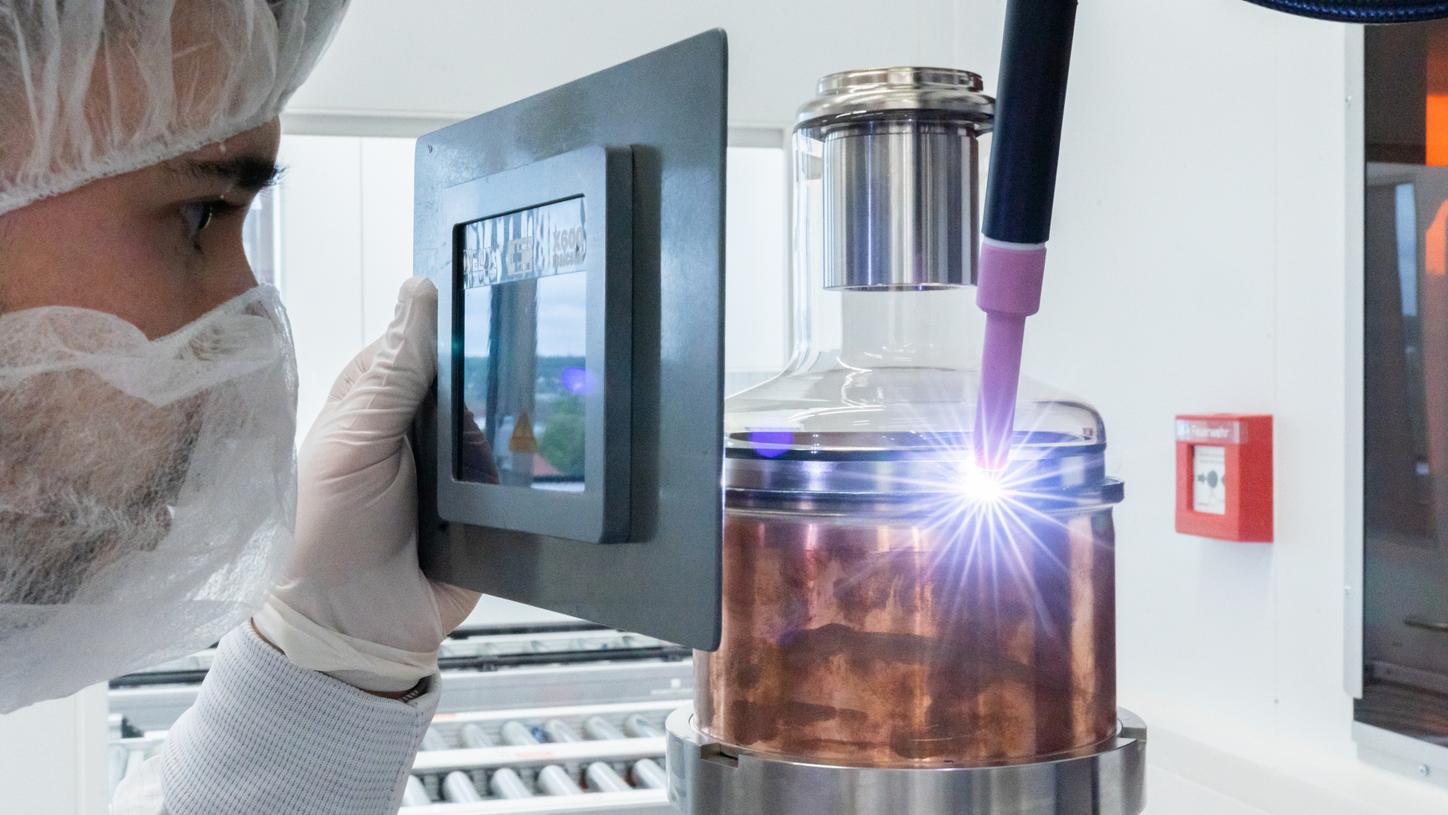
Welding on metal-glass X-ray tubes under clean room conditions.
Download image
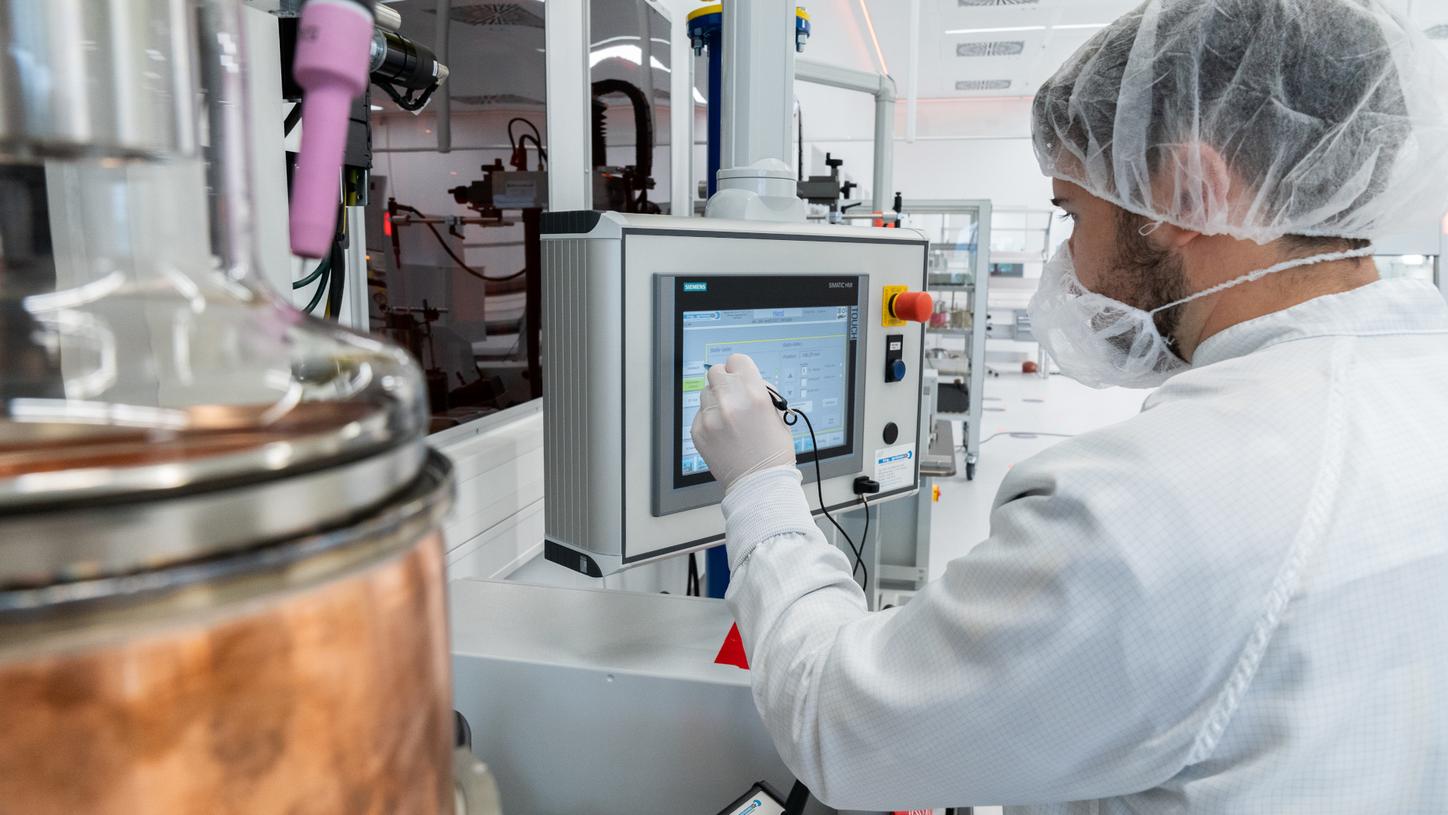
Programming the welding machine in the clean room.
Download image
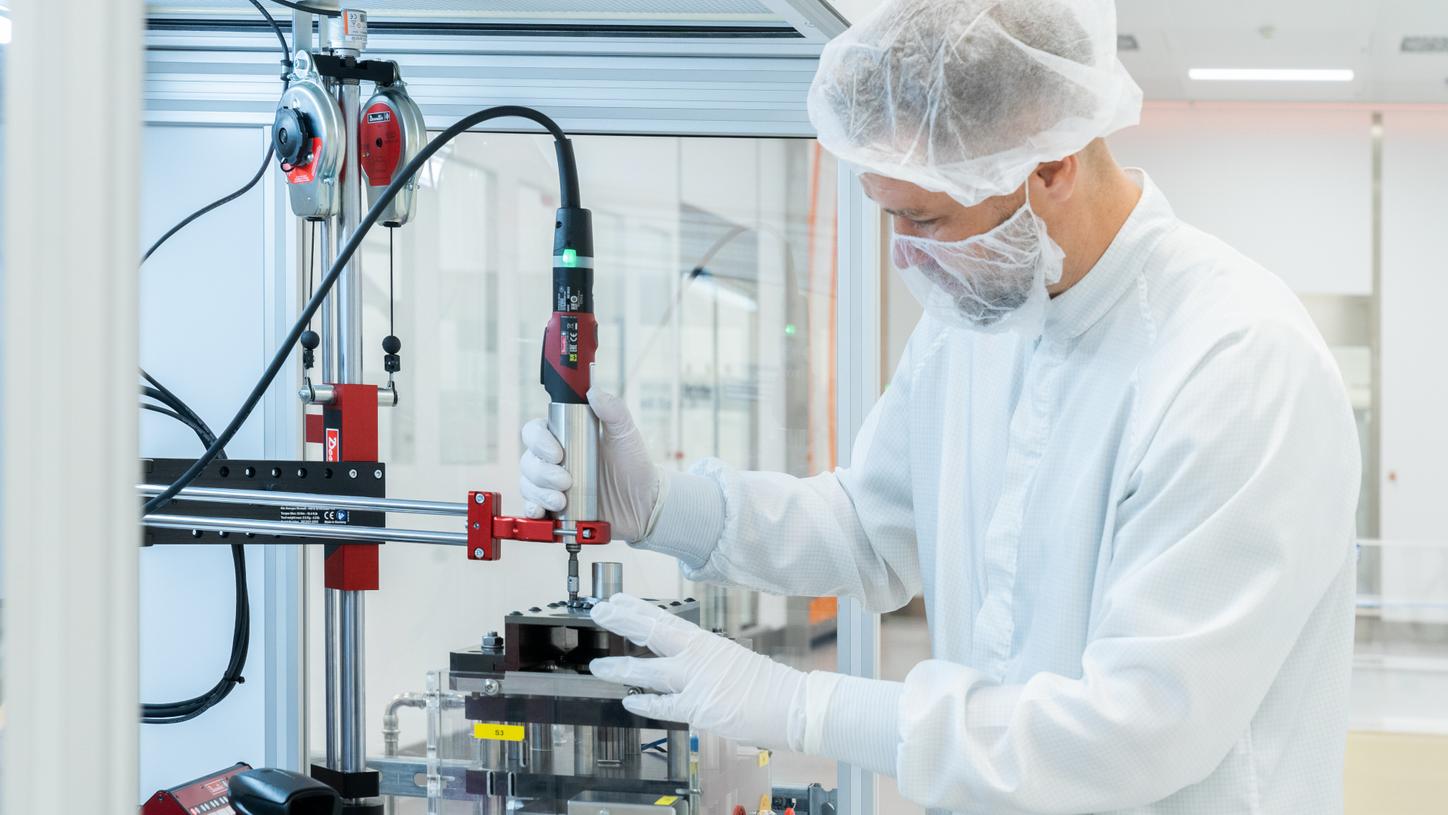
Assembly of components of X-ray tubes in the clean room.
Download image
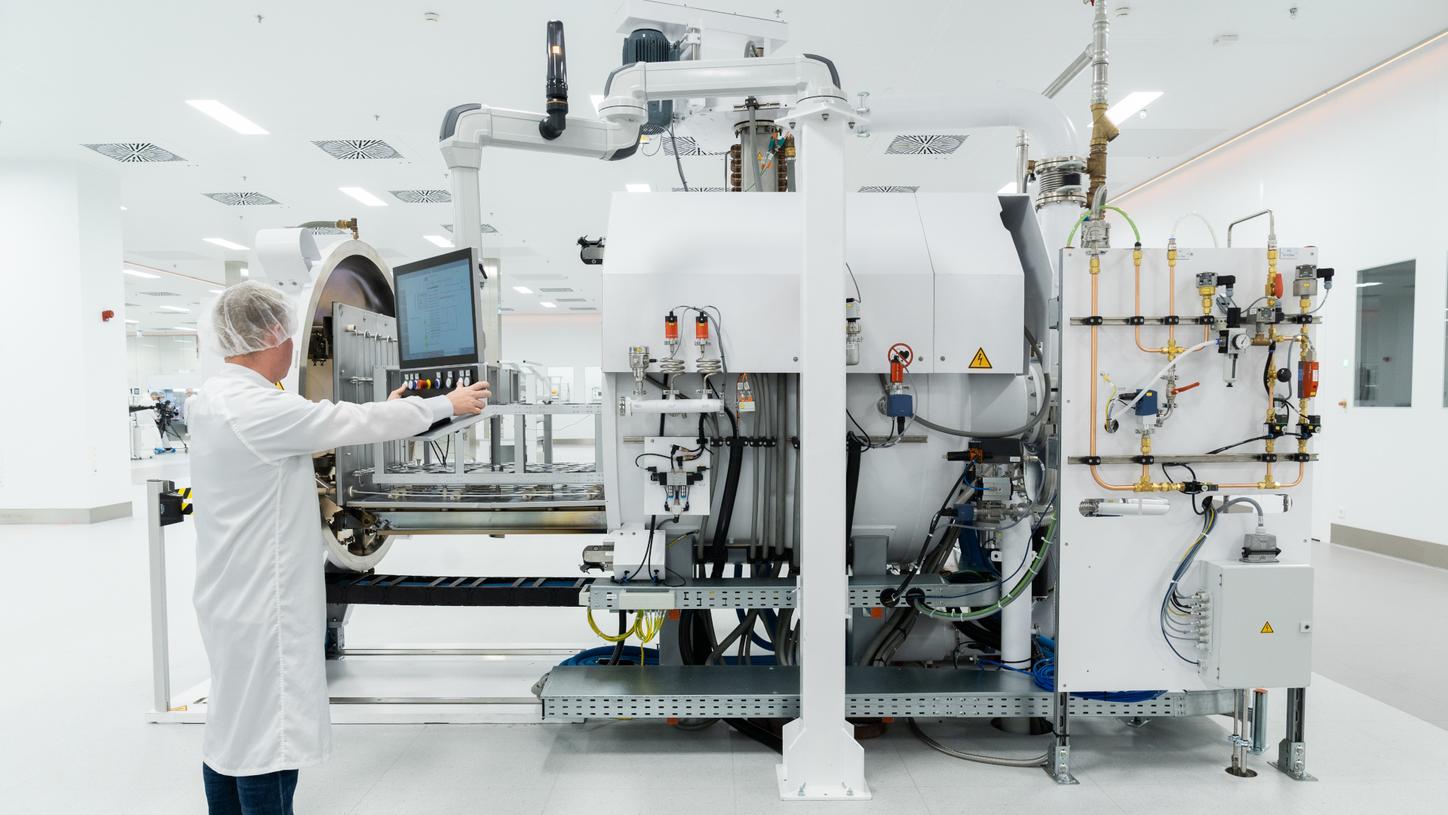
Equipping and programming a special furnace for heat treatment.
Download image
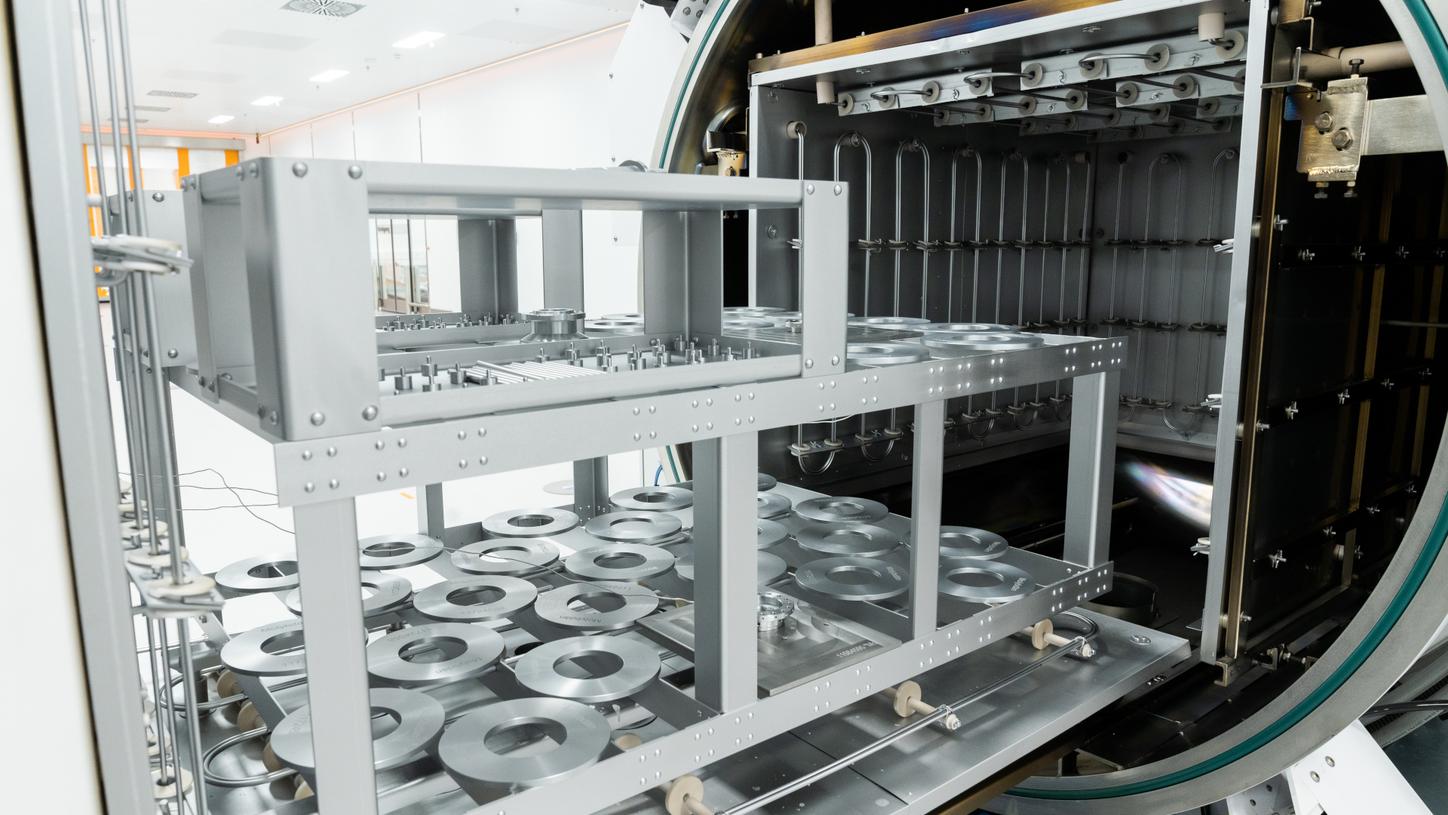
Equipping a special furnace for metal treatment.
Download image
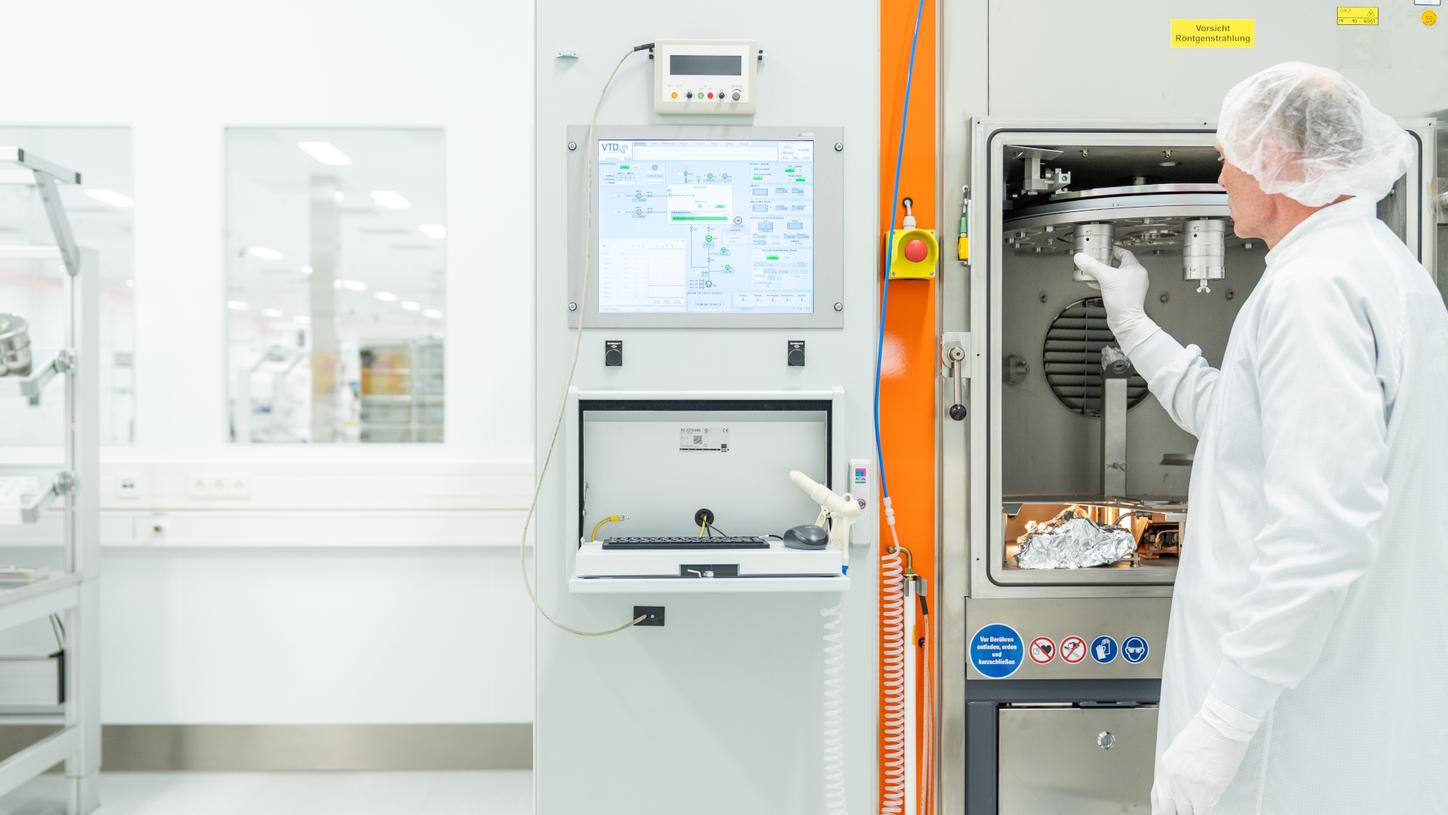
Thermal treatment of components of X-ray tubes in a special vacuum furnace.
Download image
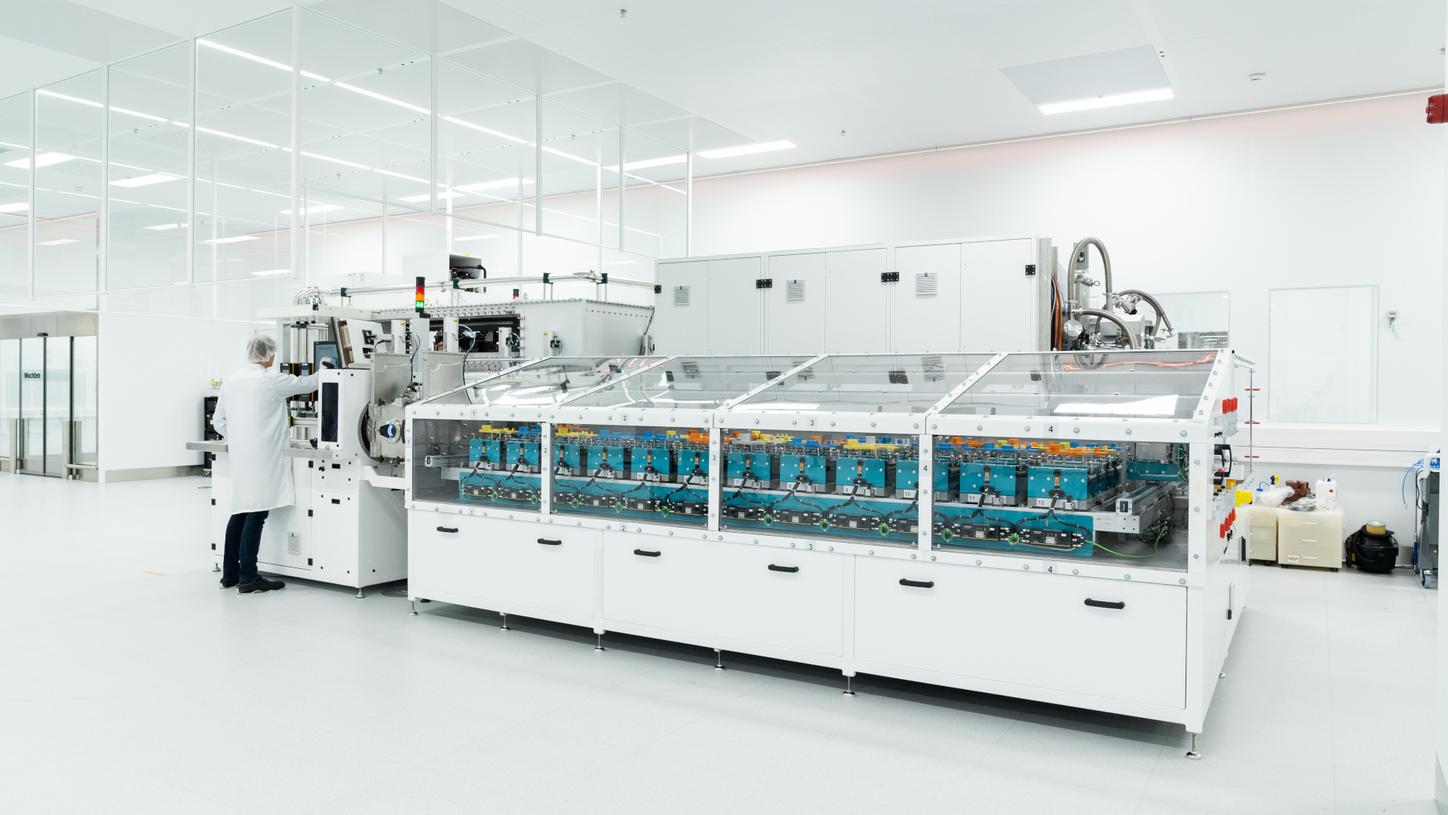
In-house developed system for the assembly of components of X-ray tubes.
Download image
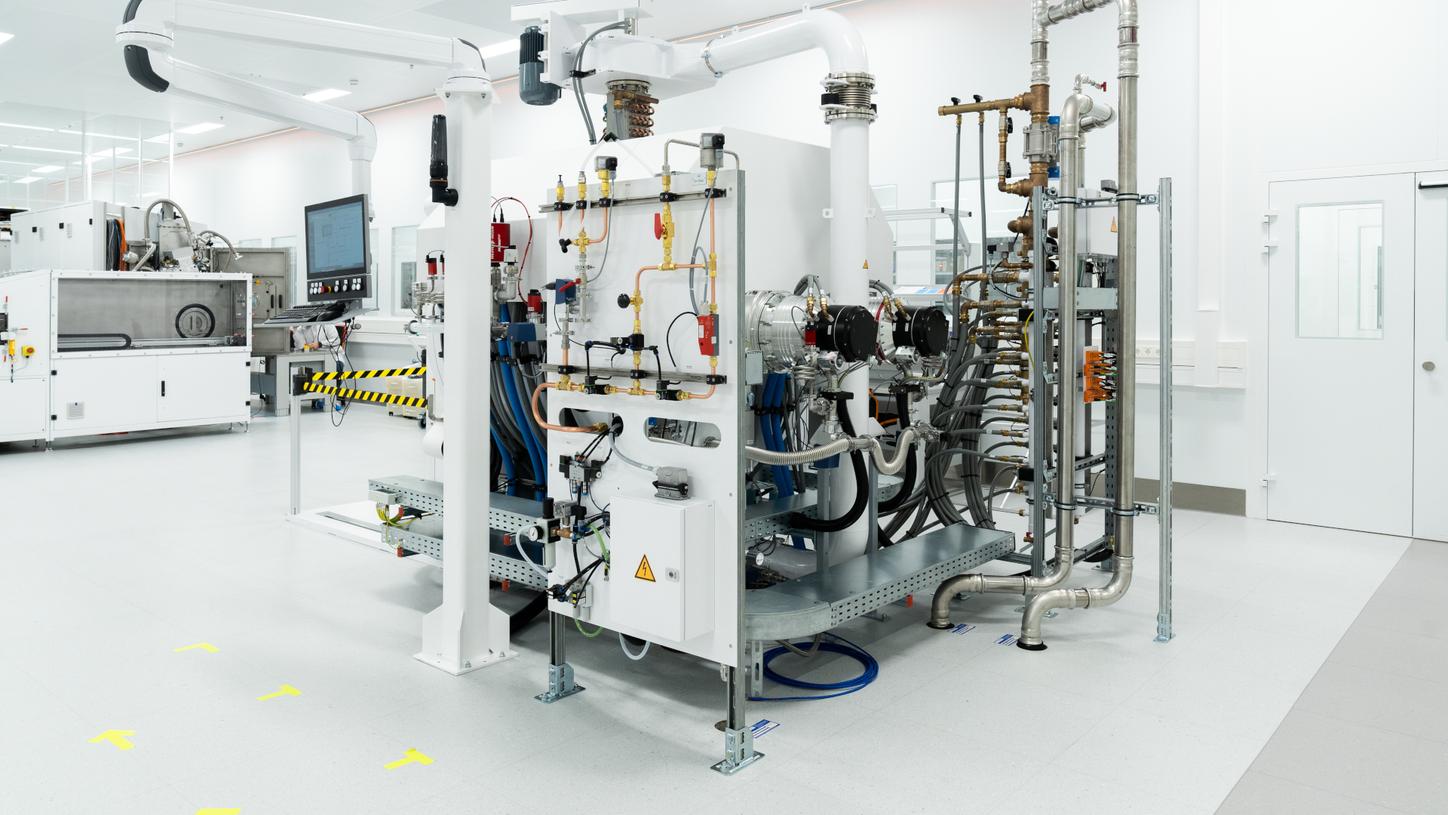
Special oven for the thermal treatment of metal components in clean rooms.
Download image
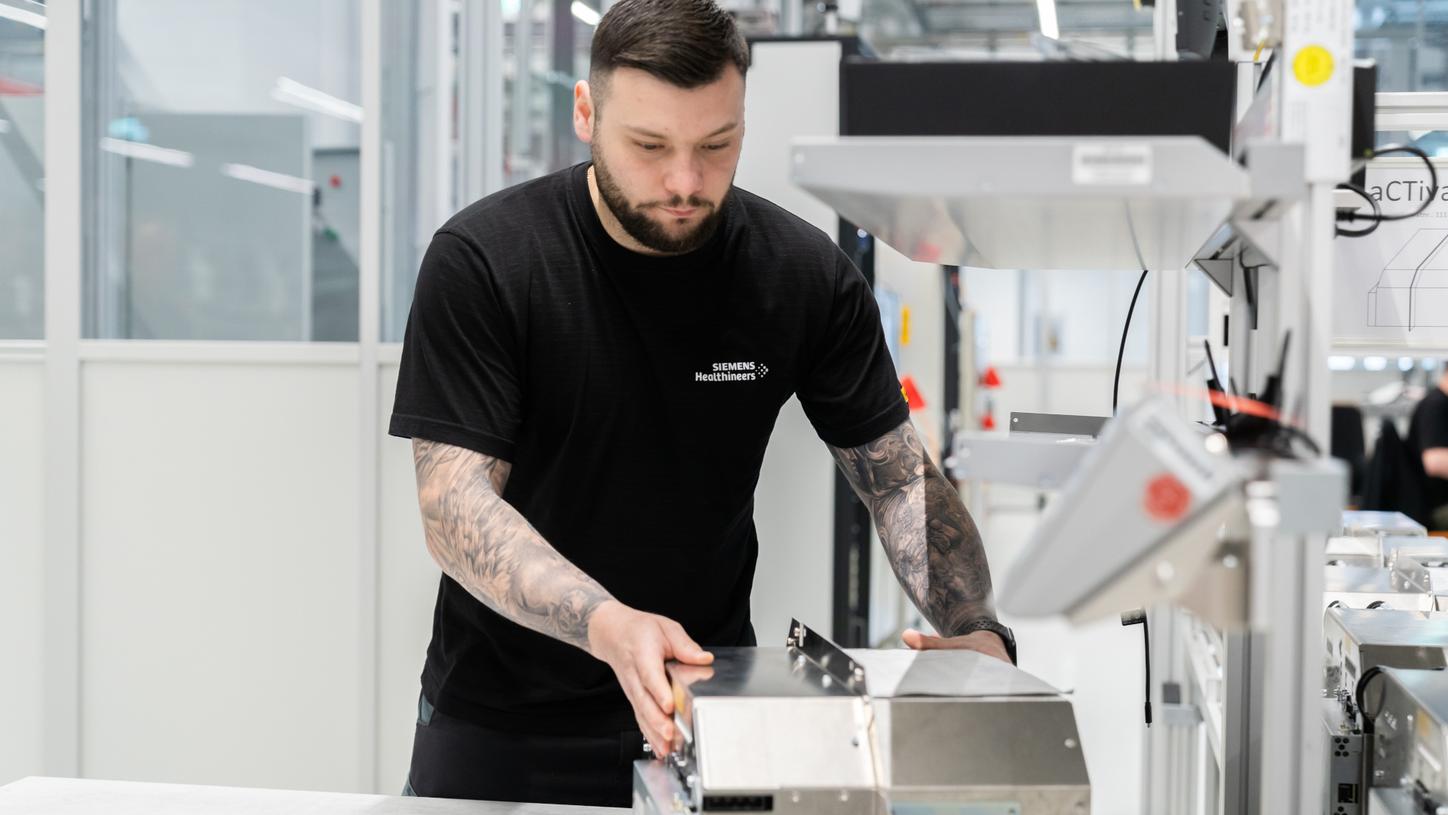
Assembly of housing parts for the high-voltage supply of X-ray tube assemblies.
Download image
Videos
Background, sustainability, and regional significance
With a €350 million investment, the construction of the HEP Center is Siemens Healthineers' largest single investment in new construction, highlighting Forchheim's importance. About 700 employees are expected to work at the center.
The HEP Center covers 69,000 square meters and operate nearly CO2-neutral. The energy concept utilizes waste heat from production processes and recovers heat through cooling systems. Photovoltaic systems on the rooftops, highly efficient heat pumps, and the procurement of green energy are expected to reduce CO2 emissions to nearly zero. Additionally, regional and recyclable building materials are being used to minimize pollutant emissions.
The HEP Center plays a crucial role within Siemens Healthineers by providing the "Smart Engine" for the company's most successful imaging devices, including CT, X-ray, angiography, and mammography systems. These advancements contribute to significant improvements in medical diagnostics and treatment, such as faster and more accurate breast cancer screening and minimally invasive cancer treatments.
Siemens Healthineers employs about 11,000 people in the Erlangen/Forchheim area. Forchheim serves as the global headquarters for the Diagnostic Imaging and Advanced Therapies business units and is the main development and manufacturing site for computed tomography, X-ray, and angiography systems. The expansion of the Forchheim site will enable the company to increase and optimize manufacturing capacities in the region, maintaining and enhancing its global leadership position in diagnostic imaging.
Figures:
- Gross Floor Area about 69,000 m² (prod. 50,000 m², office 17,000 m², Central Utility Building 1,900 m²)
- Length 216 m x width 76 m x height 24 m
- 3 production floors, 6 office floors, 1 technical floor
- About 800 workplaces
- Entrance area with bistro/café open to the public
- Green building certification LEED “silver”
- Photovoltaics on the roof: 1.5 GWh/a
- All Electric Concept enables CO2-neutral operation of the HEP, Avoidance of approx. 11,000 t CO2/a
Presentations of media day
Power & Vacuum Products – Technology Center @ Siemens Healthineers
Horst Schmidt (Head of Power & Vaccum)
Power & Vacuum Products is a division of Siemens Healthineers that specializes in the development and production of high-performance generators and vacuum components for various medical applications.
High Energy Photonics Center Digital Lighthouse - Our journey to our first digital native factory
Dr. Markus Kaupper, Head of Digitalization
From formerly two locations, ONE digital lighthouse is emerging: the HEP Center in Forchheim. Siemens Healthineers is pursuing a comprehensive digitalization and automation approach across the entire product lifecycle.
Expert Talk Digital Twin: From requirements to designs and execution: Combining lifecycles of product and production
Peter Wittmann, Marcel Eisenbeiß
The technology of the digital twin enables the behavior and performance of the real counterpart to be simulated and analyzed in a digital environment. At the HEP Center, Siemens Healthineers uses the digital twin even before the first groundbreaking to optimize and secure modern manufacturing facilities, the integrated production processes, and the overall construction realization.
Expert Talk Data & AI: Optimizing performance: About connectivity, data backbone & AI
Tobias Grüner - Head of Process Data Management & Andreas Selmaier – Data Solution Architect
Siemens Healthineers relies on connectivity, data backbone, and AI to optimize performance at the HEP Center. Through end-to-end integration, the value of data can be maximized and utilized in the digital twin, from the delivery of parts to the finished product at the customer. Thus, data and AI have great strategic importance in improving efficiency and responsiveness in production.
What’s coming next? Our Journey to our first digital native factory
Dr. Jens Fürst, MBA, Principal Key Expert A&D
Dr. Markus Kaupper, Head of Digitalization
Siemens Healthineers is driving digital transformation in medical technology, utilizing the innovative technology of the digital twin. The HEP Center is becoming the first "Digital Native" factory, setting new benchmarks in production with the use of digital twins. This enhances efficiency, improves product quality, and thus creates a future-proof, resilient, and sustainable production environment.